
Four global megatrends are reshaping tomorrow’s factory, according to a study by Frost & Sullivan’s Manufacturing Leadership Council (https://goo.gl/y86rFT).
Aligned in encompassing categories – globalization/urbanization/regionalization/ uncertainty, smart/material/open/green, business model innovations, and ambient intelligence – these trends represent the forces that “will prompt manufacturers to rethink not just factory design but how production processes and infrastructure can support a wide range of new opportunities made possible by digitization.”
Digitization should be familiar to Aerospace Manufacturing and Design readers – Big Data, Industry 4.0, the Industrial Internet of Things (IIoT) all involve the collection, distribution, and analysis of growing streams of 0s and 1s.
The “Vision 2030: The Factory of the Future” study predicts that in the next 10 to 15 years, the factory will be an integrated hardware and software system “fueled by vast quantities of information from every corner of the enterprise and beyond. Manufacturers will replace large, centralized plants with networks of smaller, more nimble factories that are better able to customize production for specific regions and customers.”
In a recent online post, Jeffrey Moad – research director and executive editor with Frost & Sullivan’s Manufacturing Leadership Community and co-author of the study – zeroed-in on aerospace: “Smart, connected products and real-time analytics will allow manufacturers to sell outcomes such as jet engine uptime and not just products. This means manufacturers will need to fundamentally rethink their relationships with customers. It also means they will face an entirely new competitive landscape.”
I asked Moad how he sees this trend extending to other parts of the aerospace supply chain, not just to jet engine manufacturers performing service as part of years-long maintenance, repair, and overhaul (MRO) contracts. He answered that those outcomes- and services-based business models will ripple out, “redefining not just who does the maintenance, but who owns, finances, and takes responsibility for the performance and safety of the asset in the field.”
We’ve seen this outcome model in the growth of leasing companies owning aircraft and centralizing those responsibilities, as well as ride-sharing apps for terrestrial transportation that decentralize ownership and maintenance obligations. Providing positive outcomes will apply to products as well as services.
“The ongoing trend to add intelligence and connectivity to assets in the field will mean all participants in the value chain – not just the original equipment manufacturer (OEM) – will have access to detailed and timely information on how products are used and how they can be improved,” Moad says.
As tier suppliers collect and act on reliable data generated by smart products and analytics, they will be able to understand and respond to end customers’ needs. Translating that understanding into better products and services will require new levels of design, supply chain, and production collaboration.
“Producing to print won’t be good enough anymore,” Moad explains.
I agree with the study’s executive summary: “Many manufacturers will have to undertake significant cultural, organizational, and management changes if they are going to take advantage of the opportunities offered by the digital revolution.”
Please let me know if you are undertaking such changes to stay on the crest of the emerging digital wave. – Eric
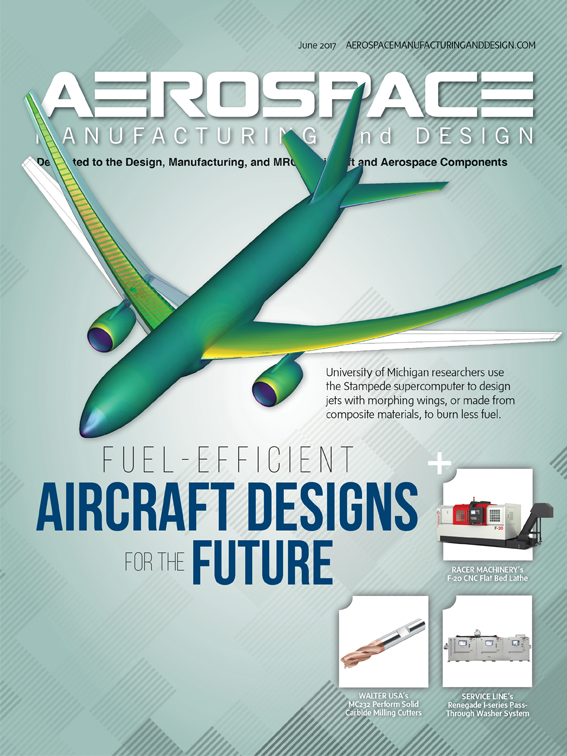
Explore the June 2017 Issue
Check out more from this issue and find you next story to read.
Latest from Aerospace Manufacturing and Design
- Webinar: Successfully navigate Industry 4.0
- SMW Autoblok answers your questions June 20
- Supply Chain Management in Aerospace Manufacturing
- Airbus, Avincis partner on advanced air mobility
- Monaghan Tooling Group's Vergnano P-Series Taps
- IMTS 2024 Conference: Sustainability in Manufacturing - Now What?
- Intuitive Machines lands on the moon using Sciaky EBAM-made part
- Kyocera's PR20 Series insert coating technology for grooving applications