_fmt.jpg)
Year-end holiday air travel returned to near pre-pandemic levels despite passengers needing to wear masks in terminals and on aircraft, proof of vaccination requirements at destinations, and flight delays or cancellations due to staffing shortages. Increased demand for air travel and air cargo is spurring new aircraft orders and freighter conversions – but expect hiccups along the way. Variations in the COVID-19 virus have led to spikes in infections and hospitalizations, supply chain bottlenecks remain, and concerns that 5G wireless service introduction near U.S. airports could interfere with aircraft radar altimeters and disrupt travel all confound experts’ predictions for when normal will return.
Airbus delivered 611 commercial aircraft to 88 customers in 2021, 8% higher than 2020.
In 2021, Airbus doubled its gross order intake compared to 2020 with 771 new sales (507 net) across all programs, and at the end of 2021, Airbus’ backlog stood at 7,082 aircraft.
“The year saw significant orders from airlines worldwide, signaling confidence in the sustainable growth of air travel post-COVID,” Airbus CEO Guillaume Faury says. “While uncertainties remain, we’re on track to lift production through 2022 to meet our customers’ requirements.”
The A220 won 64 firm gross new orders and several high-profile commitments. The A320neo family won 661 gross new orders. In the widebodies, Airbus won 46 gross new orders including 30 A330s and 16 A350s of which 11 were for the newly launched A350F (freighter) which also gained an additional 11 commitments.
Airbus deliveries 2021 vs. 2020
Program | 2021 | 2020 |
---|---|---|
A220 family | 50 | 38 |
A320 family | 483 | 446 |
A330 family | 18 | 19 |
A350 family | 55 | 59 |
A380 | 5 | 4 |
Total | 11 | 566 |

Boeing’s year-end results were unavailable at press time, but Boeing officials did release 2021 delivery figures for its commercial airplanes and defense programs.
Boeing 2021 commercial aircraft deliveries
Program | Deliveries |
---|---|
737 | 263 |
747 | 7 |
767 | 32 |
777 | 24 |
787 | 14 |
Total | 340 |
Since the Federal Aviation Administration (FAA) approved the 737 MAX’s return to operations in November 2020, Boeing has delivered more than 195 of the aircraft and airlines have returned to service more than 200 previously grounded airplanes. The 737 program is producing at a rate of 19 per month, progressing toward a 31 per month production rate early in 2022. The company’s still evaluating the timing of further rate increases.
Acknowledging the inspections and rework halting 787 deliveries, Boeing management expects the current 787 production rate of approximately two airplanes per month to continue until deliveries resume and then return to five per month.
Commercial Airplanes’ backlog includes more than 4,100 aircraft valued at $290 billion.
Boeing delivered 83 new and remanufactured AH-64 Apache and 20 new and renewed CH-47 Chinook helicopters, 16 F-15 and 21 F/A-18 fighters, 13 767-derived KC-46 tankers, and 16 737-derived P-8 maritime patrol aircraft – numbers about even or slightly up from the previous year. Backlog at Defense, Space, & Security was $58 billion; 33% represents orders from customers outside the U.S.
Boeing President and CEO Dave Calhoun told associates in late October, “As demand returns, supply chain capacity and global trade will be key drivers of our industry and the global economy’s recovery.” He also noted, “We’re increasing freighter production and conversion capacity to meet the robust and fast-growing demand for air cargo due to the surge in e-commerce. Between new and converted freighter orders this year, we have already surpassed the highest annual freighter order tally in our history.”
Calhoun emphasized the company was “advancing technologies and digital manufacturing capabilities to drive our next generation of products and a more sustainable future.” He added the company was evaluating the timing of a freighter version of the 777X and beginning to lay the foundation for Boeing’s next commercial airplane development program.
Lockheed Martin’s F-35 program continued to expand its global footprint and enhance operational capabilities. In 2021, Switzerland and Finland selected the F-35 for their new fighter jet programs, Denmark received its first F-35, and the Royal Netherlands Air Force became the ninth nation to declare their F-35 fleet ready for initial operational capability.
Numerous program achievements are enabled by employing digital technologies, credited with achieving 142 deliveries in 2021. Smart tools, connected machines, and augmented realities all contribute to the delivery and sustainment of aircraft.
“Lockheed Martin is investing in digital technology that advances the F-35’s 5th Gen capabilities long after delivery,” says Bridget Lauderdale, vice president and general manager of the F-35 program. “We’re embracing digital transformation to enable faster development and continuous deployment of software, using digital models and supercomputers to augment physical test data with simulation-based verification, and automating data processes to save time and glean insights that improve sustainment.”
More than 750 F-35 aircraft operate from 30 bases and ships around the globe, with 12 services having declared initial operational capability.
Embraer delivered 32 commercial jets and 54 executive jets (36 light/18 large) by the end of Q3 2021 (the latest figures available). The 86 aircraft delivered exceeded the 59 total aircraft delivered during the same period in 2020. Total company firm-order backlog was $16.8 billion, up from $15.1 billion the year before. This is the highest quarter-end backlog value for Embraer since the end of 2019, driven largely by executive aviation orders.

The company reiterates its deliveries guidance for 2021 of commercial jet deliveries of 45 to 50 aircraft, executive jet deliveries of 90 to 95 aircraft.
Embraer also reported Q3 revenue grew in its services & support and defense & security segments, up 29.7% and 14.1% on a year-over-year basis, respectively. Commercial aviation revenue grew 36.6% year-over-year to $242 million, and executive aviation revenues were 20.8% higher than the same period the prior year, to $ 256.4 million.
Teal Group predicts civilian unmanned aerial systems (UAS) purchases will reach $121 billion throughout the next decade. Non-military UAS production will jump from $5.6 billion a year to $18.9 billion by 2030, a 14.1% compound annual growth rate in constant dollars.
Drone delivery is expected to be the leading sector in the U.S. by 2030, with industrial inspection emerging as a major commercial drone market.
Industry insiders
Richard Aboulafia, FRAeS Managing Director, AeroDynamic Advisory
A speedy recovery, for most segments
The COVID-19 pandemic has been a catastrophe for aviation. Aircraft deliveries fell 35% in 2020 from 2019, while world air travel demand fell 66%. These numbers are completely unprecedented.
Yet there are reasons for cautious optimism. According to preliminary year-end numbers, the industry grew 7.5% in 2021. And 2022 should see 22% expansion.
First, military deliveries were hit last year for logistical reasons alone – pandemic related factory closures and supply chain disruptions. Actual demand wasn’t hit at all. Countries that initially announced pandemic-related defense budget cuts reversed those plans, and actually increased spending from the previous year.
Defense demand is strong, both for geopolitical reasons and because defense spending is viewed as a good way for governments to support aerospace industries in a difficult time. Military output will fully recover to pre-pandemic levels in 2022, with more growth after that.
Business aircraft have also come back fast, with utilization recently passing 2019 peak levels. Corporate profits, equities markets, and oil prices, the three big drivers behind demand, are all at very high levels, coupled with strong interest in avoiding the service cutbacks and high load factors of airline transport. Delivery numbers are recovering accordingly, and we’ll see a return to 2019 peak levels (in units) next year.
Jetliners – normally accounting for around 60% of total industry output – are overall in good shape. We expect air traffic to return to its 2019 peak in early 2023. Fuel prices are back from record lows, while jetliner financing costs remain quite low. This ratio – the cost of fuel to the cost of capital – is the most important determinant of jetliner market health after airline traffic – the market does best when expensive (but not too expensive) fuel means airlines want to replace older jets, and when there’s inexpensive financing available for those new jets. The ratio today looks excellent.
The largest industry segment is single aisle jetliners. Deliveries increased by more than 40% in 2021 and will increase another 40+% in 2022. This is largely driven by the very strong domestic market recovery we’ve seen in North America and China. Twin aisle jets are the only exception to this positive jetliner outlook.
There are still risks, most obviously in the form of another COVID-19 variant. But as of now, the COVID-19 aviation downturn will likely be remembered as shorter-lived and more isolated than originally feared. After falling off a cliff, the industry is ready to rebound fast.
Sean Holt, President of the Americas, Sandvik Coromant
The effects of the COVID-19 pandemic are still impacting businesses, whose struggles this year will center on staffing and resource management. Even as the industry continues to recover, many businesses face labor shortages and see current staff, who hold critical expertise, continuing to leave the workforce. We see them bridging the gaps that result in two ways: engineering services and digital solutions.
Engineering services upskill workforces – Many businesses are turning to engineering services to extend their teams and upskill current employees. Provided primarily by tool suppliers such as Sandvik Coromant, these engineering teams are one facet of global engineering centers. They’re experts who offer on-demand support to a company’s staff, either virtually or on-site.
Sandvik Coromant’s engineering service team works alongside a company’s staff, mentoring them in areas most needed. Depending on the business, those needs vary; our team has shared machining best practices, equipment recommendations, tool selection, CAM programming, fixturing, and more. These high-demand services, sought out by original equipment manufacturers (OEMs) and the supply chain, are set to increase as businesses look for instant support on their terms that maintains efficiencies in their entire manufacturing chain, not just their cutting tools.
Digital solutions improve decision-making – To improve efficiency and resource management, digitalization is becoming more prevalent among companies of all sizes. Both large OEMs and small-to medium-sized manufacturers (SMEs) are investing in Industry 4.0 infrastructure that monitors performance and captures real-time data that informs decision-making.
Machine and cutting tools, along with components, fixtures, and add-on systems, are being digitally transformed and set up for data capture. We’re seeing engineers shift from drawings to computer models of entire processes and workflows. Optimized processes improve efficiency, and access to real-time data and insights enable better, fast decision-making that can help companies remain competitive and reliably achieve their goals.
Gisbert Ledvon, Director Business Development Machine Tool, Heidenhain Corp.
As evidenced by an uptick in sales of complex contouring controls and questions from those in the aerospace industry, we at Heidenhain see the trend of next-level 5-axis machining increasing in 2022 and beyond.
Industry 4.0 aspects will be addressed by new, intuitive machine setup with smart probing functions. A user will customize and adapt the CNC screen’s content based on the specific application and related tasks, always seeing exactly what’s important. Personalized settings in the user administration function can be set within the newest CNCs including operator access level to protect programs and cutting data changes. And with Heidenhain’s latest control offerings, the new internal human machine interface (HMI) offers intuitive operating solutions for everyday production tasks – including complete integration of program testing with high-resolution simulation of the machining process in Programming mode. The user can rotate 3D images, select functions, and navigate, all with dynamic tapping and swiping gestures right on the touchscreen.
The digital twin will evolve with more graphical support for aligning the workholding equipment using new Dynamic Collision Monitoring functions. This allows a seamless import of 3D model files into the CNC for real process verification before and during machining. Real cutting time estimates based on specific machine dynamics allow precise estimation for a single or large lot size of production parts.
Integrated process monitoring in the CNC with a constant 3D view of the machining quality is now possible. This allows a visualized direct comparison between a reference part and production part on the CNC, without adding additional sensors to the machine tool and using data from the motion control system in real time.
Heidenhain’s TNC 7 control offers advanced machining features to produce parts more accurately and quicker.
In-process inspection includes visual inspection of the cutting tool on the CNC while using Heidenhain’s VT 121 camera, helping users identify a broken tool within one second during tool rotation. The cutting tool images can be stored and adapted for documentation purposes. The tool remains in the machine while the images are recorded to minimize inspection time. These images can also be called up remotely to optimize NC programs and replace tools. The technology prevents expensive rework because tool inspection can take place before executing critical machining steps.
The next level of machine monitoring will complete process reliability. New functionalities such as job management, digital maintenance manager, tool life management, and real-time notification systems based on problem codes will help manufacturers improve machine and resource utilization across several CNC platforms using MTConnect, OPC-UA in 2022, and beyond.
Markus Stolmar, President and CEO, United Grinding North America
COVID-19 is still here, and so is Zoom. We’re closing in on two years dealing with the pandemic. Travel in the U.S. has largely returned (2.3 million passengers during Thanksgiving 2021), but there’s still less business and international travel. For business travel, a long-term effect is already underway. Remote work is here to stay, and a lot can be done virtually where a flight was needed in the past. This evolution should be mitigated a bit by people who are yearning for vacations, but it’s still significant.
Market shifts are coming. New materials have entered the aerospace market. Carbon fiber reinforced ultra-high temperature ceramic (UHTC) composites are one such material. They’re resistant to corrosion, oxidation, and wear, while having better thermal properties. It can only help in making more efficient aerospace components. Also, industry forecasters such as Richard Aboulafia project twin-aisle aircraft won’t grow due to the lull in international travel. Instead, single-aisle planes and their route flexibility will see an uptick. Think 200 seats, capable of a flight over the Atlantic.
Combination machining will be crucial. Airlines are always looking for ways to save, and that’s especially true in these times. Combination machining – one machine capable of grinding, milling, and more – will help them realize those savings.
United Grinding North America works closely with manufacturers at all levels of the aerospace supply chain, helping to develop processes and provide technology for challenging applications and difficult-to-machine materials. Automation is poised to be a grinding game-changer, and the in-house automation team at United Grinding helps manufacturers maximize productivity with ideal solutions, whether custom-built or standard.
Drew Shemenski, President, WENZEL America
The COVID-19 pandemic, starting in early 2020, put a fast and brutal end to the growth enjoyed by aerospace manufacturing during the previous several years. An industry that was poised for continued growth was now faced with a crisis that compounded the challenges inherent to modern manufacturing. Workforce development, and accessibility to labor, are two of the biggest issues facing aerospace manufacturing and require a concerted effort from the entire industry to create sustainable solutions that will foster growth.
The need to develop the next generation of workers is nothing new, but cultural shifts leading young workers away from manufacturing careers have accelerated with the effects of the pandemic. To change this, local outreach with education partners is a critical part of any manufacturer’s development plan. Apprenticeships, MFGDAY events, and sponsorship of robotics teams are tools we can use to build manufacturing career interest in our future workforce. We’re fortunate to have support from our county officials and our local school districts for these types of partnerships which help us collaborate with our customers and competitors to help address workforce development needs.
In the near term, however, we need to put more workers on the floor. Population and demographic shifts, wage escalation, and simple competition are factors that strain the ability to recruit workers. This creates the need for a two-pronged strategy, worker retention, and redistribution of labor.
Investing in workers with continuing education is key to retaining talent. Whether sharpening existing technical skills, or re-educating workers for new roles, there exists a tremendous opportunity for training that can be tailored to companies’ needs. A curriculum such as AUKOM is a great example of training that can benefit the entire manufacturing and quality team and is also likely eligible for local grants and subsidies. Many companies also have success partnering with local community colleges, which can have a rich assortment of training programs at the ready.
Finally, it’s paramount that manufacturers of all levels embrace the variety of affordable automation solutions available. Automation isn’t just for high volume production, or large companies. There are solutions for every budget and industry need, helping companies drive efficiency and profit while freeing up talent to focus on creating new products or solutions for customers.
2022 will be a pivotal year for aerospace manufacturing and will lay the foundation for future growth. If we learned anything in the past few years, it’s that our predictions can sometimes be off. Here’s to hoping that 2022 has all the positive outcomes we need, and fewer surprises.
Bernie McConnell, Executive Vice President – Commercial, Greenleaf Corp.
Critical for success in 2022:
Talent retention – Maintaining a happy, healthy, and productive workforce is always top of mind for business leaders; but in today’s environment with more than 11 million job openings, and unemployment at record lows, this must be your primary focus. Stay close to your employees and make sure they know how valuable they are to the company’s overall success, and that their daily work truly has a positive impact on our world. You can’t take care of customers’ needs if you don’t have motivated people to answer the call.

Inventory management – Given the volatility within the supply chain, raw material shortages and rapid inflation, it’s critical to manage inventory like your future success depends on it… because it does! Take a balanced approach to making sure your company has sufficient raw materials that are mission critical, while looking for and lining up alternatives if needed. Having backup suppliers is also a good idea in case your regular suppliers fall short and can’t deliver. Have adequate supply of your own finished goods inventory to react quickly to increasing demand as markets recover around the world. Market share growth opportunities will come your way if you have the product and can deliver on time.
Emerging new technologies – Staying fresh and current with new technologies such as additive manufacturing is also key in this rapidly changing society. Being engaged in the industry, networking with experts, and working with leading customers is the best way to be a part of the conversation. You learn by doing, so push your teams into difficult situations and watch them thrive as they take on new perspectives. You never know, it could lead to your next new breakthrough product.
Dr. Michael Shepard, Vice President, Aerospace & Defense, 3D Systems
Consider the aerospace sector’s manufacturing and design prospects for the year ahead from an additive manufacturing (AM) perspective.
Continued impacts of COVID-19 pandemic – The world will continue feeling the impacts of the pandemic. This suggests the widespread supply chain difficulties in 2021 will persist in 2022, but there’s the prospect that conditions will ease in the back half of the year as global markets adjust to the new normal. I anticipate aerospace organizations implementing new approaches to logistics, and even pockets of vertical (re)integration as manufacturing capabilities are in-sourced to maintain control of key processes. Additive manufacturing (AM) will likely play a key role in easing supply chain issues. Moving forward, AM can be expected to enable fully automated digital manufacturing workflows to accelerate production applications – producing increasingly complex parts quickly and efficiently.
Space launch innovation – Commercialization and democratization of space continues. New entrants and established organizations are working aggressively to lower launch costs. The design, performance, and supply chain challenges associated with space launch hardware, particularly rocket engines, are ready-made for AM solutions as it allows designers to build intricate, highly unitized designs with an exceptionally streamlined supply chain.
Radio frequency (RF) passive hardware – Recently, RF engineers have begun to apply AM to RF components. Engineers are no longer limited by conventional manufacturing and assembly processes and have greater flexibility to tailor their RF components for performance and system-wide efficiency. The benefits can be profound – improved RF performance, reduced weight & volume, and large reductions in part count through unitization.
Hypersonics – New capabilities are desired in military aviation. R&D efforts are underway to produce weight-efficient, highly optimized components fit for service in the most extreme hypersonic environments. AM is uniquely suited for these challenges, offering dramatic design flexibility and rapid production of flight-worthy hardware.
Vytis Zalimas, CEO, JetMS Regional
Uncertainty over inflation and interest rates, increasing energy and oil costs, the demand for growing salaries, and the process of sourcing suitably qualified employees in the industry will all heavily impact the future of the maintenance, repair, and overhaul (MRO) sector.
The MRO market is facing a major labor scarcity and the lost competencies that go with it, forcing many companies to instigate new strategies to attract new talent.
A way of lessening the impact of any labor shortage is through digitalization and technologies such as enterprise resource planning (ERP) systems designed to better utilize materials, labor forces, and time management.
In early 2020, many in the aviation industry feared for the future of their livelihoods. However, as has already been visibly demonstrated, aviation is driven by dedicated professionals with the ability to find opportunity even in the darkest scenarios.
We believe that the smaller players in the industry should actively cooperate, merge, and grow in unison as a means of establishing themselves as vital and competitive players in the market. We maintain that mergers and acquisitions build real value and create companies that can become meaningful players right across the entire aviation industry.
Pat Waddick, President of Innovation and Operations, Cirrus Aircraft
The economic environment impacts on labor and supply chain are felt industry wide and we’re not immune to these challenges. Cirrus Aircraft is continuing to invest and expand to enhance the customer experience, improve productivity and efficiency, invite new people into aviation, and ultimately deliver more aircraft and services. Cirrus Aircraft is anticipating continued supply chain volatility for the next 12 to 18 months. Demand is robust, placing a growing burden on the entire supply chain and Cirrus Aircraft is working to mitigate these challenges.
David Ziegler, Vice President Aerospace & Defense Industry, Dassault Systèmes
Supplier-created parts and content now represent 50%-to-60% of the value of an aerospace system. Relentless price pressures are compelling aircraft manufacturers and suppliers to reinvent how they work with the supply chain. Otherwise, aircraft manufacturers who can’t find strong suppliers may seek to acquire and insource high value suppliers.
The aerospace supply chain can transform from a siloed and linear supply chain to a value network to improve visibility, on-time delivery, and right-first-time quality.
Only digital platforms offer companies new ways to conceptualize, design, manufacture, test, certify and sustain new vehicles, accelerate business, and become more competitive.
Digital platforms provide one single environment that increases transparency and enhances collaboration across organizations and locations by ensuring full access to knowledge, know-how, skills, and talents, and by enabling real-time collaboration between individuals, groups, or organizations.
With robust models and processes embodied in an enduring secure authoritative source of truth throughout the systems life cycle, digital platforms provide a framework to model every aspect of a mission and system of system complexities.
Digital platforms integrate technology, processes, and people throughout the product development life cycle for the development of advanced, complex, capable and competitive systems that are first to market.
Original equipment manufacturers (OEMs) and suppliers are undergoing a shift to compete quickly and effectively in a transforming market driven by an unrelenting pace of innovation. Digital platforms enable them to break down silos, accelerate program maturity, drive flexible production, and create new business opportunities to deliver new experiences that propel the industry higher.
Edward Talerico, Aerospace & Defense Product Manager, Infor
Trends to watch in 2022:
Cybersecurity compliance – The changes in industry regulations will continue to be a challenge. Enterprises that don’t already have a C-level compliance officer will add the role to the organization chart, along with a designated budget. With increasing pressure to comply with strict mandates, more companies will come to the same conclusion: Cloud deployment is the best way to protect critical data. Solutions in the Cloud are highly secure, with the host company overseeing back-ups and vigilantly protecting against breaches.
Digitalizing aftermarket service – As more companies turned to aftermarket service and maintenance during 2021 – and will continue to do so in 2022 – the need for digitalization is clear. Companies relying on maintenance, repair, and overhaul (MRO) revenue will invest in Cloud-based service management solutions so they can apply data insights to boost productivity and optimize resources. Smart enterprise resource planning (ERP) solutions will play an important role in improving operational efficiencies, such as parts inventory and technician scheduling.
Workforce recruitment, retention – The severe shortage of right-skilled workers is reaching crisis status, as companies in aerospace and defense (A&D) and other technology-intensive companies are competing for the same talent. A recent workforce study found that many A&D companies have floundered at bringing diversity to their workforce, even though 73% say that a policy of diversity, equality, and inclusion is a company priority. As organizations try to broaden their recruiting efforts, they’ll turn to talent science solutions to help. While technology alone can’t fix a complex problem overnight, it can help collect data, apply objective analytics, and help leadership set goals and track improvements.
Suraj Patil, Assistant Manager, Aranca
The aerospace industry has always been an early adopter of innovative and disruptive technologies. Here are five technology trends that could impact aerospace manufacturing.
Quantum technology – Quantum bit’s ability to hold 0, 1, or 2 states simultaneously (superposition) can speed up computation exponentially. Leading players in the aerospace industry are currently focusing R&D efforts on three areas:
- Quantum communication: Quantum Key Distribution (QKD) could make the communication infrastructure safer for aerospace platforms.
- Quantum computing: Cryogenic technologies for qubit systems, including cryogenic digital logic [such as single-flux-quantum (SFQ) technology and superconducting microwave components], are under study to increase their scalability. This would enhance their applicability in various areas.
- Quantum sensors: New microwave bolometer, the most advanced quantum sensor, uses graphene to detect infrared radiation at high speeds with high sensitivity.
Model-based digital engineering – Applying model simulation across functionalities allows for innovative techniques, especially from system conception to retrial, thereby speeding up execution.
- Digital twin: By integrating virtual representation and synchronized real-time data, digital twin enhances the accuracy of prediction. This helps in accurate projection of lifespan, improves performance, and increases savings.
- Digital thread: It’s the digitized record of a system’s traceability across the life cycle and for taking informed decisions.
About the author: Eric Brothers is senior editor of Aerospace Manufacturing and Design. He can be reached at ebrothers@gie.net.
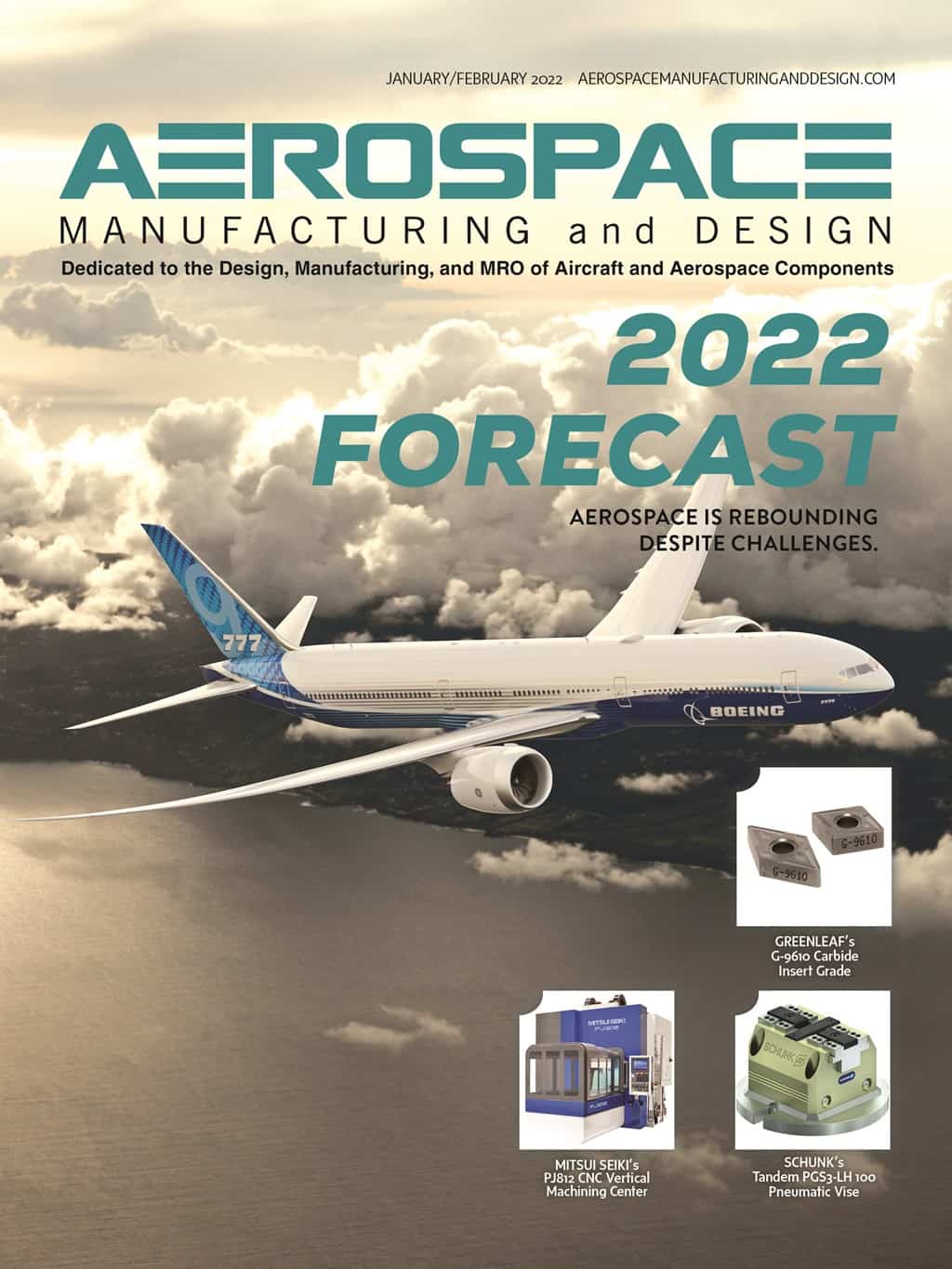
Explore the January February 2022 Issue
Check out more from this issue and find your next story to read.
Latest from Aerospace Manufacturing and Design
- JEKTA, ZeroAvia partner on hydrogen-electric amphibious aircraft
- Mastercam 2025 software
- IMTS 2024 Conference: Cutting Edge Innovations: Maximizing Productivity and Best Practices with Superabrasives
- Eve Air Mobility unveils first full-scale eVTOL prototype
- Dillon Manufacturing's Fast-Trac Jaw Nuts
- IMTS 2024 Conference: Breaking the Tradeoff: Utilizing Deep Learning AI with X-ray Computed Tomography for Unparalleled Clarity and Speed
- #47 - Manufacturing Matters - The Ins and Outs of CMMC 2.0 with Smithers Information Security Services
- Qatar Airways orders 20 more Boeing 777-9s