
Components that convey fuel, air, and hydraulic fluid in aerospace vehicles, equipment, and other applications are safety critical, so top quality manufacturing is a must. So when Connecticut-based supplier E.A. Patten Co. looks to improve productivity and competitiveness, it focuses on areas that won’t touch its quality and safety records. A key target for those process improvements are time-consuming roughing activities.
“It’s all in the roughing. In a nutshell, the more efficient roughing is, the better the overall cycle time is going to be,” says E.A. Patten Senior CNC Programmer Roger Dimmock.
To improve roughing efficiency, E.A. Patten machinists apply Dynamic Motion CNC strategies of Mastercam CAD/CAM software from CNC Software Inc., Tolland, Connecticut. The programming tools provide high metal removal rates, minimize cycle times, maximize tool life, and exploit the full capabilities of machine tools. Toolpath algorithms continuously manage tool engagement by monitoring material removed and cutting conditions – controlling feeds, speeds, and toolpaths to maintain an ideal, constant chip load. Cutters move in arcs and circles, and avoid tight corners and deep tool engagements that magnify tool pressures. Unconventional toolpaths reduce lateral forces and heat that accelerate tool and machine wear and can damage workpieces. Dynamic Motion technology is applicable to milling operations including facing, contouring, pocketing, and 3D roughing, as well as rough turning.

Radial chip thinning
The software’s algorithms allow radial chip thinning, which calls for higher cutting speeds and feeds when cutter engagement falls below 50% of tool diameter – maintaining a constant chip load and optimal cutting temperatures. The increased cutting parameters improve productivity, and the lighter cuts decrease tool wear. Lower cutting forces enable high metal removal rates, even when machining delicate, thin-walled parts; holding the parts in weaker fixtures; using less powerful machine tools; or operating tools at long extensions.
Dimmock says he was skeptical when software reseller Macdac Engineering Inc.’s Alan Duprey recommended unfamiliar Dynamic Motion techniques. However, use of the technology has reduced cycle times 30% to 50% in most applications.
“Depending on what type of tools we use, I’ve even seen times reduced 70% in some applications,” Dimmock says.
Despite learning how to apply atypical parameters for Dynamic Motion machining, Dimmock says, “Working with the reseller and Mastercam, tech support was easy. If you know the basic Mastercam program, you’re taking it a step further. The software has to know the stock boundaries and avoid regions, and the rest takes care of itself. Once stock boundaries are entered, Mastercam figures everything else out.”
Dimmock describes Dynamic Motion as an evolution of peel milling techniques in which the tool takes a small radial depth of cut, and a large axial depth of cut, at faster feed rates and higher spindle speeds and nibbles away at the part.
“It is important to consider how much you can take off in one cut,” Dimmock says. The machinability of the workpiece material generally determines the appropriate stepover or percentage of the tool diameter that should be engaged in the workpiece. “In Inconel, I can take 5%, in stainless I can go up to 15% or 20%. The high-temp alloys and titanium are harder to cut. You can’t just plow through them,” Dimmock says.
He relies on tool supplier recommendations to determine the optimum amount of engagement for a particular tool in a particular material. “OSG is one brand we use and they’ve got a brochure that says you can take X-percent stepover in a certain material, depending on the tool diameter and axial depth of cut involved,” he explains.
Additional benefits

Lower Dynamic Motion cutting forces offer advantages beyond longer tool life.
“The increased parameters don’t put so much strain on the machine,” Dimmock says. “Even though the X- and Y-axis are moving faster, it’s not putting too much load on the spindle and there is less pressure on the part.”
Dimmock points out that total machine horsepower usually makes little difference, because the software-guided process involves lighter cuts and reduced tool pressures. Even so, the machine tool control must possess enough computing power and memory to process the large amount of code and have sufficient spindle speed and axis movement capabilities for the cutting parameters the Dynamic Motion program dictates.
Reduced machining forces can permit use of less cumbersome and complex workholding arrangements, speeding setup times, in some cases providing greater tool access to the part. Smaller-diameter tools may be applied for better access to tight part features and lower tool costs. However, it generally is necessary to employ high-performance tools with sufficient rigidity and hardness to cut accurately at high spindle speeds.

“You probably also want to use high-helix end mills that will push the chips out of the part,” Dimmock says. Chip removal is important because uncontrolled chips can obstruct the cutting process, accelerate tool wear, and scar the workpiece. High-pressure coolant will help clear chips, but lower-temperature Dynamic Motion machining can reduce the need for heat evacuation with coolant.
E.A. Patten machinists most often apply Dynamic Motion technology for milling but occasionally use it when turning irregularly shaped parts.
“I’ve used it turning bowling-pin shaped parts,” Dimmock says, “things that have some grooves and valleys to them. The software makes turning cuts in both directions using a button-nose cutter that swings around to cut to the right and left and swoops back and forth. It beats the old-fashioned groove-and-plunge style tooling methods.”
Whether applied in milling or turning, Dimmock says a key element of the benefits of Dynamic Motion technology is control of tool engagement. “What ruins a tool is the motion in and out of engagement. When you keep a tool in constant engagement, you get a lot more life out of it.”
E.A. Patten Co.
Macdac Engineering Inc.
Mastercam (CNC Software Inc.
OSG USA LLC
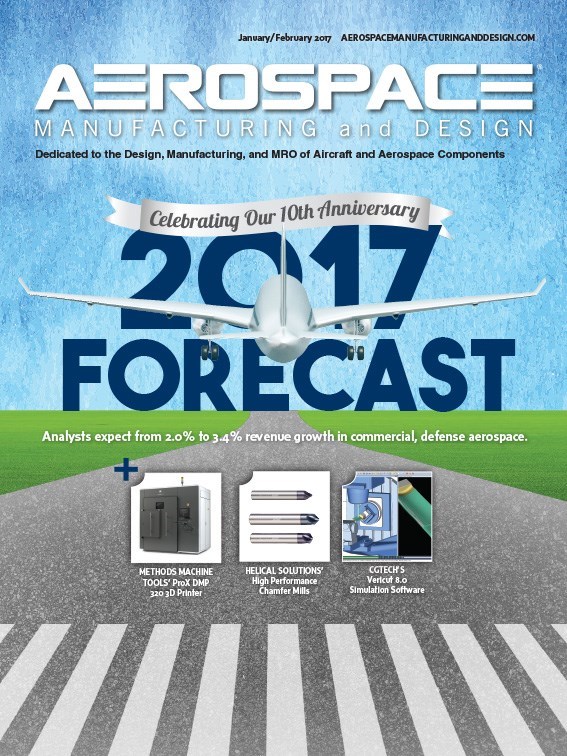
Explore the January February 2017 Issue
Check out more from this issue and find you next story to read.
Latest from Aerospace Manufacturing and Design
- Latest advancements in machine tool technology
- Visit Okuma America at IMTS 2024
- AM for Aircraft Cockpit Interior Components
- Piasecki Aircraft reveals hydrogen-powered UAM progress
- Siemens' Simatic Workstation
- Heart Aerospace to open US R&D hub
- Comau's S-Family of small industrial robots
- GrindingHub: a showcase for international grinding technology