
A technology promising to someday revolutionize manufacturing is artificial intelligence (AI). If you’re thinking of a humanoid robot watching people to learn a simple task, you’re missing a more immediate application of AI in manufacturing – metrology. Surprised?
Advances in imaging technology, software, and computing power are making it easier to automate observation, identification, and reporting of flaws on parts, which improves quality in manufacturing.
Dr. Jonathan Lee leads research and development (R&D) for Nanotronics, a science technology company that developed a system combining AI, automation, and sophisticated imaging to detect manufacturing flaws and anomalies.
I asked what’s changed to propel his company and others toward a marketable solution enabling AI-assisted part inspection. Is it better cameras? Stitching software? Smarter and faster data crunching? Well, it’s all of those.
Lee answers, “Year-on-year improvements in the price and performance of commodity hardware are making ever more complex models and processing practical. As costs come down, there are more installations, and that brings in larger data volumes, driving the creation of more specialized models, and increasing customer confidence in deploying AI and automation.”
At Nanotronics, they study human-machine interactions and assembly processes with automated tools, and feed that back into design and process changes.
“We enable our customers to enhance their own efforts to maintain effective process control, and to tighten the loop between detecting some defect, determining its source, and ultimately mitigating any issues,” Lee says. The company’s nSpec product combines advanced computer vision, machine learning, AI, optical microscopy, and robotics to recognize, classify, and measure nanoscopic flaws, allowing for real-time correction.
They take this further with Intelligent Factory Control (IFC), their term for combining legacy process control data, imaging, or other sensor data, and using them to reduce process variation, increase yields, reduce rework, or provide insight into the root causes of process variation.
IFC enables machines to autonomously correct irregularities in the production process, making self-inspecting, self-optimizing factories an achievable goal.
This sounds like a perfect tie-in with Industry 4.0.
Lee agrees, saying, “More data from more sources increase the likelihood that we can assign causality to issues seen in inspection. Digital twins give higher fidelity models of what should be, which permits us to be much more aggressive in detecting deviations to track and correct.” The goal is to change a production process item by item to hit required quality metrics with minimal rework, or across multiple variables rather than one feature at a time – all without needing constant human attention and supervision.
Nanotronics is building a high-tech manufacturing hub in New York’s Brooklyn Navy Yard. The new facility will allow the company’s AI researchers, computer scientists, and other experts to work with skilled machinists on a manufacturing floor. The objective is to develop innovations that will reduce a factory’s footprint, producing less waste while bolstering speed, from R&D through production. – Eric
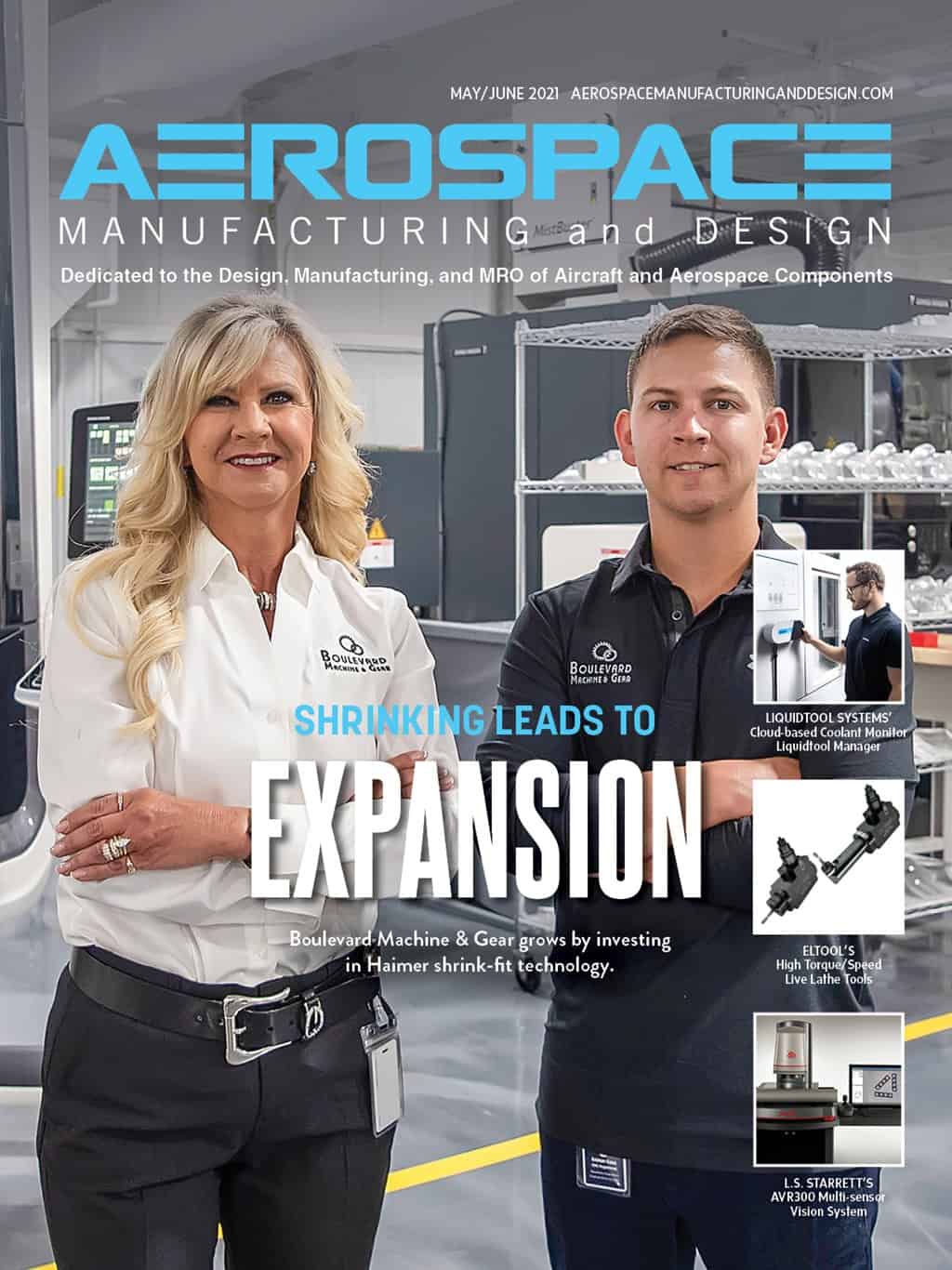
Explore the May June 2021 Issue
Check out more from this issue and find your next story to read.
Latest from Aerospace Manufacturing and Design
- Upcoming webinar to highlight the rise of electric vehicles
- JEKTA, ZeroAvia partner on hydrogen-electric amphibious aircraft
- Mastercam 2025 software
- IMTS 2024 Conference: Cutting Edge Innovations: Maximizing Productivity and Best Practices with Superabrasives
- Eve Air Mobility unveils first full-scale eVTOL prototype
- Dillon Manufacturing's Fast-Trac Jaw Nuts
- IMTS 2024 Conference: Breaking the Tradeoff: Utilizing Deep Learning AI with X-ray Computed Tomography for Unparalleled Clarity and Speed
- #47 - Manufacturing Matters - The Ins and Outs of CMMC 2.0 with Smithers Information Security Services