
Just as electric vehicles (EVs) are revolutionizing the automotive industry, electric aircraft promise to boost the sustainability and convenience of air travel. Designers of urban-air/advanced-air mobility (UAM/AAM) air taxis and electric-powered vertical-takeoff-and-landing (eVTOL) vehicles face numerous challenges when connecting high voltage (HV) and high power (HP) systems. Electrical wiring interconnection systems (EWIS) engineers and eVTOL aircraft designers are finding a wide range of solutions are now available to address these 10 connectivity challenges.
1 Significantly higher voltages (kV), power (MW)
Applying high voltage cables and power systems is nothing new for electrical engineers but applying appropriate technologies for hybrid and electric aircraft presents novel situations. By using a follow-the-wire design approach, EWIS engineers ensure all links – connectors, wiring, jackets/insulation, converters, contactors, power sharing networks, and more – handle the voltage and environmental conditions unique to electric aircraft.
- Higher voltages are found in:
- Electrical systems for conventional aircraft employ 115VAC/400Hz and 270VDC with HV power requirements, typically limited to 230VAC. In eVTOL aircraft, the thrust required across the rotor area for lift during vertical takeoff and hovering – the disc loading – necessitates fan speeds from 2,300rpm to 20,000rpm delivered by brushless 800VDC motors.
- HV alternating current (AC) is encountered in generators, power converters, and controllers employed in fast-charging stations. Other electrical differences include non-linear power-sharing networks and multi-directional charge paths.
Designing for higher voltage translates into using products with thicker dielectric materials that are heavier, stiffer, and take up more space. Advanced power wiring must allow flexibility for routing and dynamic bending of pods and wings, with optimized wiring weight, cable cross sections, and consider ribbon-type (flat) cable geometries. Respective HV connector solutions must enable current carrying capability often up to 1,000A in non-traditional connector geometries. Connectivity solutions must address the challenging power density, power frequency, and size, weight, and power (SWaP) requirements for electric aircraft.
2 Mitigation of partial discharge/corona effect
Managing HV at altitude is more complicated than on the ground. HV can ionize surrounding air particles more quickly with catastrophic effects, due to lower air densities at altitude as the less constrained particles can achieve higher velocities sooner. Released energy generates a corona discharge resulting in power losses through voids, cavities, and electrical treeing in insulation. Electrical discharges can occur across a voltage gap between two points/surfaces, because the high electrical field can’t be contained by the material(s) in the area. The discharge can also initiate electrical arcing, potentially igniting a fire. Selecting dielectric materials and constructions suited to HV conditions – such as corona-resistant polytetrafluoroethylene (PTFE) – minimizes discharge risks from insulation breakdown. Air bubbles/pockets (porosity) can be eliminated with over-molding and insert molding around connector contacts.
3 Increased reliability for harsher environment, frequent maintenance & inspection, shock, vibration

eVTOL vehicles fly shorter distances than commercial aircraft and are anticipated to make numerous takeoffs and landings per day. Interconnects need to be reliable and withstand vibration and shock from more frequent landings and take offs. Reliability is essential because eVTOLs fly over densely populated urban environments. To help ensure performance, electronic/electrical compartments need to be easily inspected. Strain relief on connectors, molded cable assemblies, and secure tie-downs can help avoid chafed components and material fatigue. High reliability connectivity products include high performance, fatigue, and stress relaxation-resilient connector materials, and redundancy in connector contact systems.
4 Premium on weight reduction
Unlike conventional aircraft that become lighter by burning fuel, eVTOL aircraft weight doesn’t diminish over distance and discharged batteries are quite literally dead weight, so EWIS designers need to calculate and carefully compare the weight of connectivity components for a given amperage and wiring architecture. Advanced, lightweight materials (plastics and composites) and 3D printing can create right-sized components for tight spaces and weight optimization.
High-efficiency relays and contactors are available to handle HV and high amperage within a compact footprint. Advanced HV relays and contactors offer voltage ratings up to 70kVDC and current ratings up to 1,000A within a useful size-to-power ratio. Compact cables, terminations, and connectors are also available for optimal size, weight, and power rating.
5 Resistance against arc tracking, hydraulic fluid
With higher voltages come unusual causes of catastrophic failure. Dust, moisture, exhaust, and other pollutants can create pathways for current to travel across a material. Electric discharges can then occur, which risk causing an explosion in flight – or on the ground when fast charging aircraft are in high moisture environments. An arc-tracking index can be used to evaluate how readily a given voltage travels across a material’s surface if it’s clean or polluted. Wire is available with dual-wall construction using radiation crosslinked modified materials that resist carbon arc tracking even when contaminated with hydraulic and de-icing fluids.
6 Strict flammability, toxicity, smoke requirements
Air inside aircraft circulates within an enclosed space, so all materials are flammability, smoke, and toxicity rated. Connectors, wiring jackets, and other insulating materials must be self-extinguishable and limit emission of toxic smoke. Silicone may be suitable for high voltages but tends to be very smokey when ignited. Halogenated flame retardants act directly against the chemistry of a flame, but the smoke can be toxic. Flame-retardant materials that are low-smoke zero halogen or low-smoke free of halogen are ideal.

7 Altitude, pressure effects
Voltage differences become extreme as altitude, temperature, and frequency increase. The conditions under which a given material supports partial discharge inception voltage (PDIV) and partial discharge extinction voltage (PDEV) can be mapped in a Paschen curve. These points can be used to determine the thickness of dielectric insulation required at specific altitudes and distances between conductive surfaces. Higher altitudes make the system more vulnerable to partial discharge and promote water seepage into gaps in components and eventual corrosion. Power switching and lightning strikes cause surges in power cable systems that can cause cable voltage to exceed PDIV momentarily, leading to insulation erosion or catastrophic failure. Using appropriate dielectric materials and design constructions that eliminate air gaps will result in designs with minimal air pressure effects.
8 Handling operating temperatures ranges, thermal management requirements
In battery charge cycles, a balance must be struck between higher energy transfer and higher temperatures. During high power charging (HPC), individual components are subjected to temperature extremes at resistance points along the HV path. Every microohm (µO) of resistance must be minimized. Areas to reduce resistance include cable terminations, contact interfaces (crimps and contact types), and contact materials. Liquid-cooled cables and laying cables in convective- or conductive-cooling heat sinks are also solutions. Thermal sensing and thermal modeling can be employed to design a cooling ecosystem for charging systems on the ground – and to detect high temperatures during power surges on landing and take-off.
9 New cabling, management, crimping techniques
Sharp edges and non-smooth conductive surfaces in HV connectors can produce concentrated voltage gradients contributing to corona discharge. Electrically sealing crimp regions smooth out surfaces and the electrical geometries to reduce voltage stress. Any change in geometry requires analysis to determine: If that edge is going to contribute to a partial discharge or corona effect, construction must be modified to mitigate that risk. HV utility power lines use circular corona rings to prevent corona losses, so rounded features can be added to HV cables to control electrical stress. Even a single loose strand of wire sticking out of a shielded cable can cause problems.
10 Accommodating high-volume production
While not directly under a EWIS engineer’s purview, designers must consider the ability of a manufacturer to handle the production, delivery, and quality of components at scale. The eVTOL market is projected to grow exponentially – and the ability to supply quality components in quantity is essential. All products should be 100% tested and inspected to ensure performance and fitness for the application. Manufacturers who can handle the tooling, supply chain, cost control, and certifications for today’s demanding aerospace and eVTOL programs can address tomorrow’s innovative electric-aircraft projects.
TE Connectivity
About the author: Matthew McAlonis is technical fellow and global leader of engineering for the aerospace defense & marine business unit at TE Connectivity. He can be reached at mmcaloni@te.com.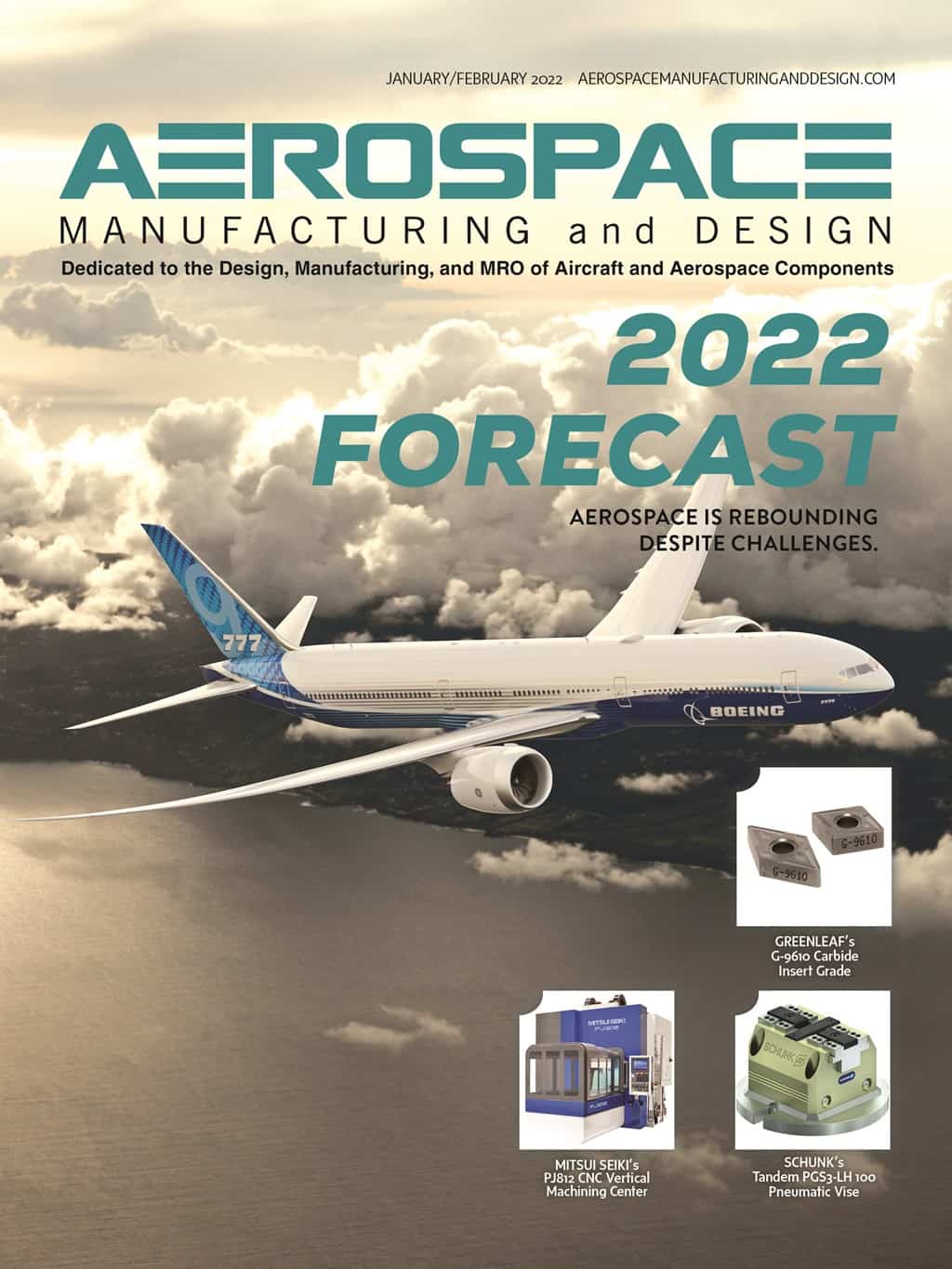
Explore the January February 2022 Issue
Check out more from this issue and find you next story to read.
Latest from Aerospace Manufacturing and Design
- Airbus UpNext launches new technological demonstrator
- HEULE's back spot facing tools
- IMTS 2024 Conference: Quoting This Way Is Killing Your Profits
- Webinar: Successfully navigate Industry 4.0
- SMW Autoblok answers your questions June 20
- Supply Chain Management in Aerospace Manufacturing
- Airbus, Avincis partner on advanced air mobility
- Monaghan Tooling Group's Vergnano P-Series Taps