
After a decade as a plastic injection and aluminum die-cast mold manufacturer, Benton Harbor, Michigan-based Shoreline Mold & Engineering started doing some aerospace work in 2005. Today, that work amounts to 60% of its business.
Shoreline’s customers use its braze, weld, bend, assembly, and checking fixtures along with braze caps made from either Inconel or Hastelloy to assemble and manufacture aircraft components.
With its early aerospace jobs, Shoreline struggled with the accuracy and setup time of a standard 3-axis CNC mill using sine plates.
“It would take half a day just to do one hole in a fixture,” says Shoreline Mold & Engineering Co-Owner and Plant Manager Bryan Fillwock. “A lot of these holes are on compound angles, so it isn’t just a simple sine plate operation. We would have to rotate and indicate the sine plate for the first angle, tip for the second angle, then pick up a tooling ball and semi-finish the hole a couple of times to sneak up on the correct location and diameter. The fixtures have multiple compound angled holes so we would have to repeat that process numerous times.”
To address precision and efficiency issues, Shoreline invited Leadwell products importer Campat Machine Tool Inc. (Elgin, Illinois), to demonstrate a Leadwell 5-axis V-40iT CNC vertical machining center (VMC).
“We had enough aerospace work to justify the 5-axis,” Fillwock says. The V-40iT significantly reduced the number of setups required for aerospace work, while increasing the features’ accuracy and machining efficiency.
“With the Leadwell, we just indicate the fixture or part square in the upright position, tilt, and rotate to the holes we want and basically just start cutting,” Fillwock explains. “Now it might take just an hour to do one hole, including setup. With the V-40iT, we can make a fixture in two setups.”
Some Shoreline aerospace fixtures have holes that enter on varying compound angles, with centerlines all intersecting a datum centerline within 0.0005" starting 3" to 4" away from the datum.
“With the V-40iT, we mounted our fixture in the machine and basically did all those holes in one setup, while pretty much relying on just the machine accuracy to put them in location to where their centerlines all intersected within 0.0005". That’s been huge,” Fillwock says.
While the parts manufactured at Shoreline don’t go inside aircraft, they must hold specific tolerances. “That’s where we’ve really improved – even on the print tolerance. They don’t even make their prints that tight,” Fillwock explains. “And when our customers use our assembly fixtures to make the parts that actually go in a jet engine, they have more tolerance to work with because we are able to hold tolerances so tight on our end. As our customers have become more comfortable with us as a vendor, we have gotten more and more work – we are expanding their tolerances in a sense.”
The fixtures Shoreline machines on the Leadwell range from a 4" x 4" window to 24" in diameter. It’s not that the V-40iT table is so large, it’s that the machine can handle it.
“While reduced setups are a reason to buy a 5-axis machine, we also prefer the Leadwell because it has a greater weight capacity on the table. It’s a much beefier machine than others we looked at,” Fillwock adds.
Shaker drums are 1.5ft x 1.0ft diameter with wavy channels that run down the sides. Shoreline mounts the drum in the machine, turns it 90°, and cuts out the channels in the 4th axis.

In addition to fixtures, Shoreline has reduced setup time for processing 1.00" x 0.75" diameter Inconel caps. Because caps distort during brazing, they can withstand only 2-to-3 brazing applications and require continual replenishment from Shoreline.
“Before we installed the V-40iT, there were 8-to-9 setups that we had to do, one at a time. It was very time consuming and hands-on. Cycle time wasn’t long enough for an operator to do anything else, so he would just be standing there switching parts in and out,” Fillwock states.
The original machining process exceeded 1 hr. per piece, required a different setup on 2-to-3 machines, and an operator to run those machines.
With the Leadwell, Shoreline got the process down to two setups.
“We stick a solid bar in the chuck in the machine, hit ‘go’, and walk away. It does 8 of those 9 setups and our run time is now 15-to-20 minutes, while the operator is free to do something else. The final setup is just taking that 90% completed piece, sticking it in a chuck or a fixture, and finishing up that last setup. It cut our time to one-third,” Fillwock says.
The reliability and solid construction of Leadwell machines further contribute to uptime and tighter tolerances.
“At least every 6 months I’m fixing a machine in the shop. I’ve gotten real familiar with all of the machines in the shop, except the Leadwell because I haven’t had to work on it. It just runs,” Fillwock says. “Leadwells are built like tanks. Everything on them is heavy-duty stainless steel except for the sheet metal on the exterior. Our V-40iT is six years old and still looks brand-new. There is not a bit of rust anywhere. Plus, it’s deadly accurate.
“We had such good luck with the V-40iT that when we needed more capacity, I didn’t even quote anything else,” Fillwock says. “I just called Campat and asked what Leadwell machine do you have and when can I get it?”
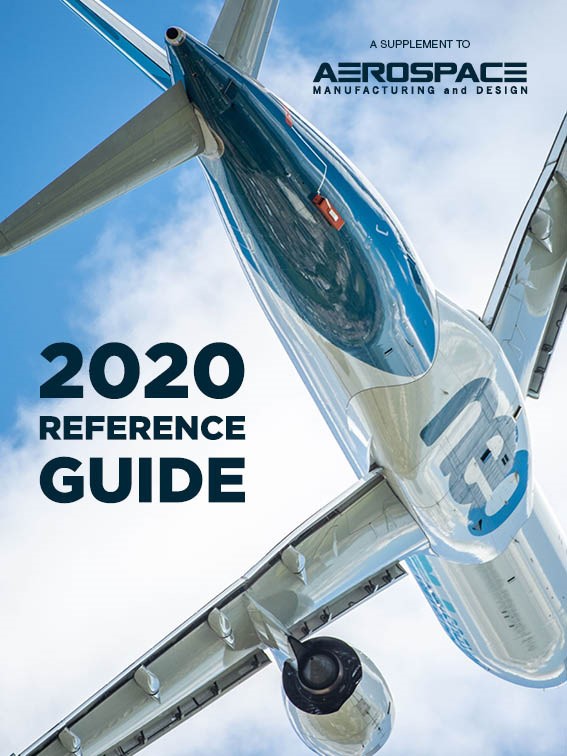
Explore the AMD Reference Guide 2020 Issue
Check out more from this issue and find your next story to read.
Latest from Aerospace Manufacturing and Design
- Upcoming webinar to highlight the rise of electric vehicles
- JEKTA, ZeroAvia partner on hydrogen-electric amphibious aircraft
- Mastercam 2025 software
- IMTS 2024 Conference: Cutting Edge Innovations: Maximizing Productivity and Best Practices with Superabrasives
- Eve Air Mobility unveils first full-scale eVTOL prototype
- Dillon Manufacturing's Fast-Trac Jaw Nuts
- IMTS 2024 Conference: Breaking the Tradeoff: Utilizing Deep Learning AI with X-ray Computed Tomography for Unparalleled Clarity and Speed
- #47 - Manufacturing Matters - The Ins and Outs of CMMC 2.0 with Smithers Information Security Services