
Rapid prototyping with on-demand laser cutting is gaining traction, offering faster, more effective ways to create aerospace sheet metal parts without needing complicated manufacturing setups. Below are four laser cutting advantages for aerospace and how SendCutSend’s e-commerce model allows it to quickly process work for original equipment manufacturers (OEMs) and tier suppliers.
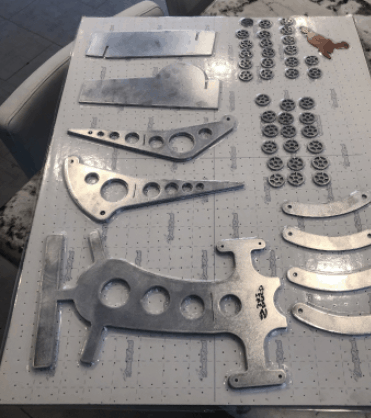
Precision cuts, increased accuracy
Laser cutting uses small, powerful lasers that deliver a focused beam of light with high precision to the material it’s cutting. The laser melts and evaporates material with 0.003" to 0.006" tolerances. In comparison, a plasma cutter usually has a tolerance of about 0.02", and most die-cutting tools have tolerances from 0.020" to 0.040". Laser cutters’ accuracy and precision make them a viable choice for aerospace, where tolerances are extremely tight.
Prototyping multiple designs
Manufacturing at scale can be expensive for aerospace manufacturers. Laser cutting allows manufacturers to test multiple design iterations in the field at low cost prior to manufacturing at scale. This method develops custom shapes and complex geometries with minimal metal distortion on completed parts. Laser-cut prototypes can be developed with a rapid turnaround for aerospace metals such as 6061-T6 aluminum, Inconel, titanium, and copper.
Cost
Laser cutting eliminates setup costs and unused parts due to design changes. You can create multiple iterations without order minimums, reducing wasted inventory. To create a component or part with a laser cutter, all that’s needed is material to cut, a laser cutter, and a schematic computer file. This significantly reduces overall costs, particularly when compared to traditional tooling and manufacturing. Laser cutters have fewer mechanical moving parts than comparable manufacturing processes, reducing maintenance and operations costs, which lowers the cost of using a laser cutting company.
Speed
A laser cutter is economical for small run projects since laser cutters don’t require custom-built or modified tooling for the application. Also, a laser doesn’t have physical cutting surfaces that wear out. Engineers can have functional parts in a couple of days, not weeks or months.
_fmt.png)

e-commerce solution
SendCutSend’s e-commerce platform allows aerospace manufacturers to get parts quickly and efficiently. Customers upload a vector file and select the metal and quantity, then the SendCutSend team reviews the file and contacts the customer with any questions. Once the project is confirmed, the file is sent to the laser for cutting and parts are shipped to the customer within three days.
One recent customer contracted SendCutSend to create assembly fixtures for a manufacturing process. Another developed prototype control panels for evaluation in simulators and ergonomic testing. Since working with SendCutSend, prototypes are developed almost as fast as they receive feedback from the testing team.

Explore the January February 2020 Issue
Check out more from this issue and find your next story to read.
Latest from Aerospace Manufacturing and Design
- Upcoming webinar to highlight the rise of electric vehicles
- JEKTA, ZeroAvia partner on hydrogen-electric amphibious aircraft
- Mastercam 2025 software
- IMTS 2024 Conference: Cutting Edge Innovations: Maximizing Productivity and Best Practices with Superabrasives
- Eve Air Mobility unveils first full-scale eVTOL prototype
- Dillon Manufacturing's Fast-Trac Jaw Nuts
- IMTS 2024 Conference: Breaking the Tradeoff: Utilizing Deep Learning AI with X-ray Computed Tomography for Unparalleled Clarity and Speed
- #47 - Manufacturing Matters - The Ins and Outs of CMMC 2.0 with Smithers Information Security Services