
KUKA Industries is part of a new project from the German Federal Ministry for Education and Research (BMBF) called ProLMD for manufacturing cost-effective, high-performance metallic components for the aerospace and automotive industries using the laser metal deposition (LMD) method. The robotics company is working with partners MTU, Airbus, Daimler, BCT, MBraun, Laserline, and the Fraunhofer Institute for Laser Technology.
“Together with our project partners, we are aiming to develop a new system solution that is based on robots,” says Günter Neumann, head of the business unit laser process solutions at KUKA Industries.
The project partners expect to achieve cost savings of up to 15% by applying various materials to complex surfaces with build-up rates of 1kg/h to 2kg/h. www.kuka.com
Liebherr-Aerospace 3D-printed flight control flies on Airbus A380

In March 2017, Airbus successfully flew a Liebherr-Aerospace & Transportation 3D-printed valve on an A380 test flight. The spoiler actuator valve block is the first 3D-printed, primary flight control hydraulic component flown on an Airbus aircraft.
Made from laser-sintered titanium powder, the valve block is part of Liebherr-Aerospace’s spoiler actuator and provides primary flight control functions on the A380. It offers the same performance as the conventional valve block made from a titanium forging but is 35% lighter and consists of fewer parts. The manufacturing process is less complex and more material-efficient than traditional milling.
Liebherr-Aerospace developed the 3D printed hydraulic component in close cooperation with Airbus and the Chemnitz University of Technology, Germany. www.liebherr.com
Large-format metal 3D printer/CNC machine

3D Hybrid Solutions Inc., a provider of metal printing tools for CNC machines, has a joint venture with Multiax to offer a large-format, 5-axis CNC machine tool with metal 3D printing speeds faster than 20 lb/h and machinable space of more than 500m3. Parts are built near-net shape with small amounts of material removal required, allowing lighter-duty CNC machines to meet the requirement. The addition of a direct energy deposition, 5-axis metal printing tool to a CNC machine allows machining of internal features and printing only what is necessary. www.3dhybridsolutions.com; www.multiax.com
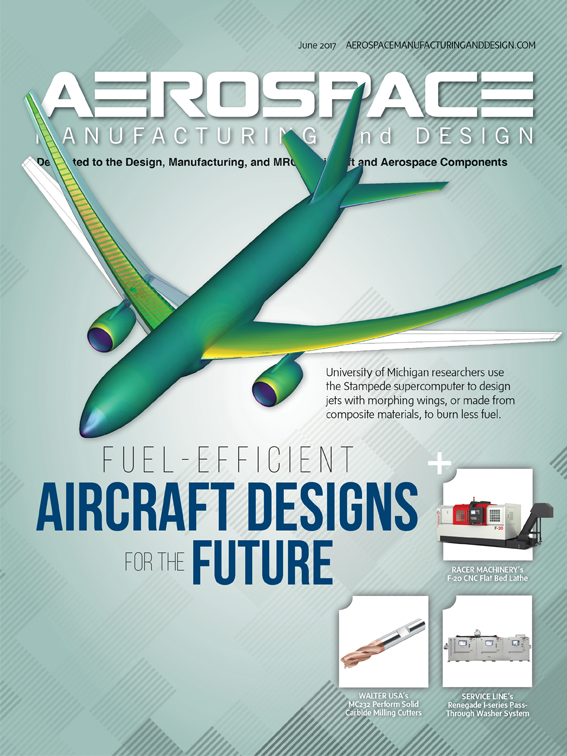
Explore the June 2017 Issue
Check out more from this issue and find your next story to read.
Latest from Aerospace Manufacturing and Design
- Upcoming webinar to highlight the rise of electric vehicles
- JEKTA, ZeroAvia partner on hydrogen-electric amphibious aircraft
- Mastercam 2025 software
- IMTS 2024 Conference: Cutting Edge Innovations: Maximizing Productivity and Best Practices with Superabrasives
- Eve Air Mobility unveils first full-scale eVTOL prototype
- Dillon Manufacturing's Fast-Trac Jaw Nuts
- IMTS 2024 Conference: Breaking the Tradeoff: Utilizing Deep Learning AI with X-ray Computed Tomography for Unparalleled Clarity and Speed
- #47 - Manufacturing Matters - The Ins and Outs of CMMC 2.0 with Smithers Information Security Services