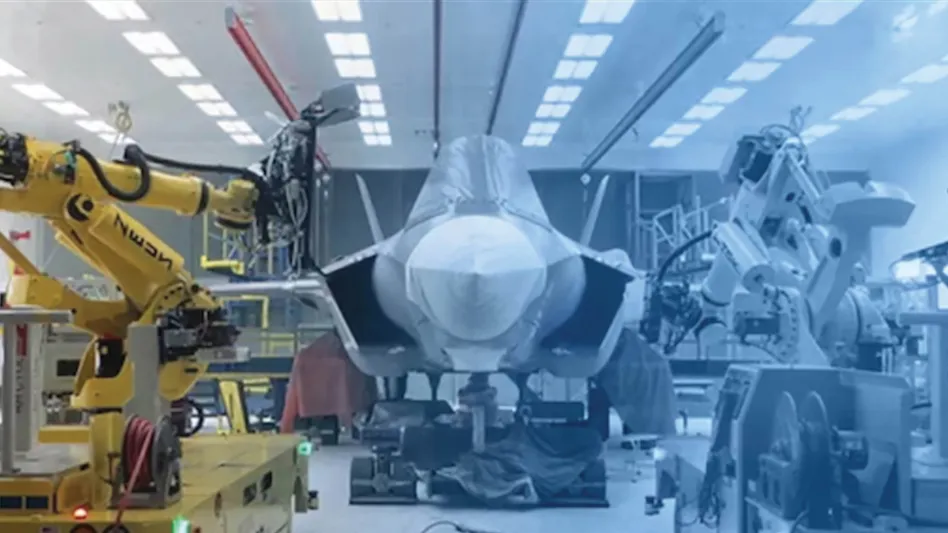
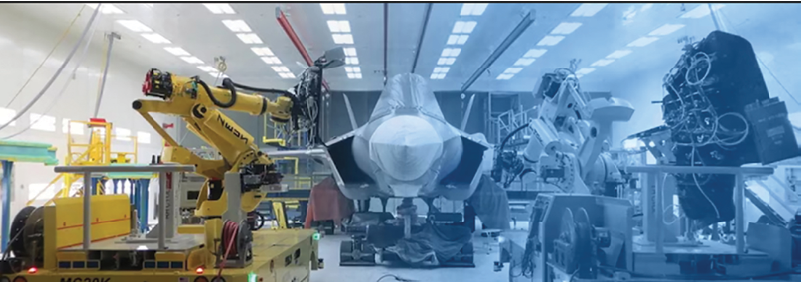
Installing an industrial robotic solution for manufacturing tasks is a significant investment. In addition to the purchase and installation, companies must budget for a risk assessment to ensure the setup will comply with Robotic Industry Association (RIA) safety standards.
Safety measures recommended in a risk assessment can be pricey – perhaps as high as $15,000 for a robot that sells in the $50,000 to $60,000 range. But companies know if they skimp on safety, they risk legal liability, insurance complications, potential shutdowns, and workers’ lives.
Financially, automated systems are a case of short-term pain for longer-term gain, but many manufacturers in aerospace and defense don’t realize how game-changing those longer-term gains can be. As an anecdotal example, a leading robotics provider recently calculated a robot they installed for $1.8 million had an operational cost of just 36 cents per hour over the life of the purchase. No human is going to work for 36 cents an hour, nor should they.
Automation ROI
It helps that for tax purposes, manufacturers can deduct the cost of large equipment using the depreciation method. For 2021 returns, small businesses could write off up to a million dollars of qualifying equipment in one year. But automation also delivers a solid return on investment (ROI) beyond tax savings.
Robots can generate cost savings via reduced labor costs and increased production efficiency. As the saying goes, time is money – especially in aerospace and defense (A&D) manufacturing – and robots have the potential to save tremendous amounts of time.
Additionally, improved quality in the manufacturing process raises ROI. Robots, when well programmed, are better at performing many tasks than humans and make fewer mistakes. These efficiencies can greatly improve the quality of work being done with less time spent correcting errors humans make, especially in fast, repetitious work.
The work is better and less expensive, and humans will have far higher job satisfaction because robots are doing the work humans don’t want to do (such as work that’s dull, dirty, and/or dangerous). For the employer, this increased worker satisfaction is likely to result in reduced employee turnover, avoiding the expenses involved in hiring and onboarding new employees.
How the Air Force saved almost $9M in six years
The U.S. Air Force has enjoyed many of the hallmarks of automation ROI since introducing a robotic painting system to restore the performance coatings on air inlet ducts for the F-22 Raptor aircraft.
On jet aircraft, inlets ensure smooth airflow into engines despite turbulent air coming at the ducts from multiple directions. The automated painting solution developed for these inlets has achieved major labor savings. The technology uses only about 300 hours of labor per unit, rather than the 1,600 hours it had taken to do the job by hand. In addition to this labor saving of around 80%, it’s estimated that since 2016, the robotic solution has saved the Air Force $8.8 million – $220,000 per aircraft – in maintenance costs.
Additionally, the automated system can apply more coating to an F-22 before the material’s pot life expires, significantly reducing waste. The highly engineered coatings cost around $1,000 per gallon, and more efficient use can save about $40,000 per aircraft. Automated painting has also improved accuracy and quality control, giving the F-22 aircraft a better performance signature against radar.
Meanwhile, the Air Force has seen workers suffer far fewer injuries. When jet-engine inlets are recoated manually, maintenance workers must wear protective suits and respirators and spend hundreds of hours crawling around on their hands and knees inside the inlet. The Air Force has reported that workers trying to apply coatings in such cramped quarters often incur shoulder injuries. Under difficult work conditions, it’s also nearly impossible for humans to manually apply the coatings at consistent speeds and thicknesses. Robots achieve better results while also curbing the number of worker injuries.
Other cost-savings case studies
Published cost-benefit analysis from other A&D organizations, and the broader manufacturing industry, have found that automated systems deliver strong ROI.
Automation reduced total labor use by up to 2.3x with a median of 1.4, and in six out of 10 cases studied, reduced total costs. The study concluded “The consistent evaluation of 10 examples showed how promising the technology already is for a range of robot types, mobility, autonomy, scale, business models, and locations.”
Another case study by Fanuc also showed the potential benefits of automation in the production process. One operational procedure for the featured integrator lowered processing times by half. There were also significant improvements in production time, and critical workpieces had their operational life extended. Machine parts that, previously, were routinely scrapped due to power shutoffs now had a longer life thanks to an automated power-failure feature that avoided operational shutdown and saved machine parts from being scrapped.
Other benefits of automated systems include that robots can run 24/7, enabling manufacturers to handle a surge in demand. Robots’ cost efficiency also breaks down the offshore argument that labor costs will be cheaper overseas. Additionally, the presence of robotic systems demonstrates to customers that a manufacturer is embracing the latest technology and can help the company secure new business.
An investment that pays for itself
Research has shown that organizations can enjoy significant cost savings and other benefits with the right robots and integration. But they shouldn’t do it alone. Finding an expert integrator to assist with development and installation is a critical component to correctly implementing any automated process.
The upfront cost can be a large investment but has compelling potential to pay for itself with a greatly increased likelihood of increased profits, consequential time and labor savings, improved output quality and workplace safety, as well as enhanced employee satisfaction and retention.
Aerobotix
D&A NEWS AND PRODUCTS
Business segment focused on automation solutions for manufacturers
Okuma America Corp. launched a new business segment created to recommend, sell, and support manufacturing production line systems composed of Okuma CNC machine tools and integrated automation technologies. The new division began operations in April 2023, and is based at Okuma America’s headquarters in Charlotte, North Carolina.
The decision to launch the Okuma Factory Automation Division was in direct response to increased demand from manufacturers seeking automated machining systems and cells for their operations to address labor shortages and to increase production capacities. Solutions will include proprietary and seamlessly integrated automation systems including automated material loading/unloading systems, machine tending and industrial robotics, automated workpiece pallet changers (APC), flexible manufacturing systems (FMS), smart manufacturing systems, and more.
Wade Anderson has been appointed the division’s new general manager. Anderson has worked for Okuma for 17 years in engineering, technical sales, sales leadership, product management, and technology partner relationships.
Okuma America Corp.
Renewed partnership
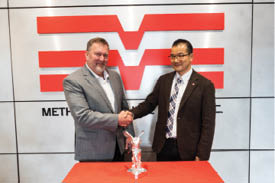
A new commercial agreement between Methods Machine Tools and Yasda Precision Tools K.K. continues Methods’ role as the single importer, distributor, and service provider of Yasda’s portfolio of precision machining centers in the U.S. The formal relationship between the two companies began in 2014, when Methods began importing Yasda’s of 3- and 5-axis lines, including the YBM vertical and horizontal series, YMC series, and the PX30i and H40i precision centers.
Methods Machine Tools
Yasda Precision Tools K.K.
Ontic signs multi-license radar, NAV/COM agreement with Honeywell
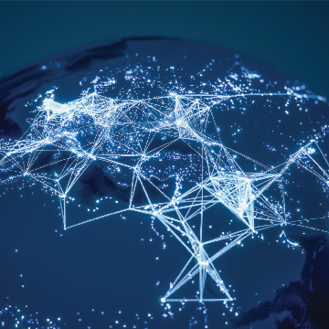
Ontic, a licensor and manufacturer of complex engineered parts for the global aerospace and defense industries, signed three new license agreements with Honeywell to deliver radar system, navigation, and communication product lines.
Ontic will take on the P440/660/880 Primus weather radar system, and the former-BendixKing’s Gold Crown, Multi-Hazard product lines, as well as heat exchangers, valves, actuators, and oil coolers for commercial and military customers.
The Primus system is used to detect hazardous weather including turbulence and wind-shear. The RDR2000/2100 series and Gold Crown product line assists navigation, communication, radar, and safety systems, enabling air-to-ground and air-to-air communication, identification, and navigation. The incorporated Multi-Hazard safety sensors perform traffic awareness (TAS) or traffic alert and collision avoidance (TCAS) and/or enhanced ground proximity warnings (EGPWS).
These systems are used across a range of aircraft, including business jets, single engine aircraft, and helicopters.
Honeywell Aerospace
Ontic
Philadelphia high school establishes advanced manufacturing program
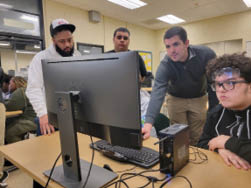
CNC Software, developers of Mastercam software, and Andrew Crowe, a manufacturing leader and speaker to the White House and Pentagon, presented Benjamin Franklin High School in Philadelphia, Pennsylvania with software, equipment, and vision to establish an advanced manufacturing program. This donation will enable students to receive the advanced training required to enter the manufacturing field after graduating high school. Mastercam provided their software, training resources, and equipment to help the students develop advanced manufacturing skills they can use to build a successful future.
Mastercam
EASTEC Booth #5249
Edge products facilitate integration into IT solutions
Software modules of the edgeConnector product family access process data in SIMATIC S7, SINUMERIK 840D, and Modbus TCP controllers. The edgeAggregator, which is also Docker-based, provides an OPC UA data integration layer in conjunction with a Docker-based Internet of Things (IoT) edge solution. This allows various OPC UA servers of the automation level to be grouped together with their associated address spaces. The aggregated data can then be made available to information technology (IT) applications via a consistent OPC UA interface.
Softing Industrial Automation
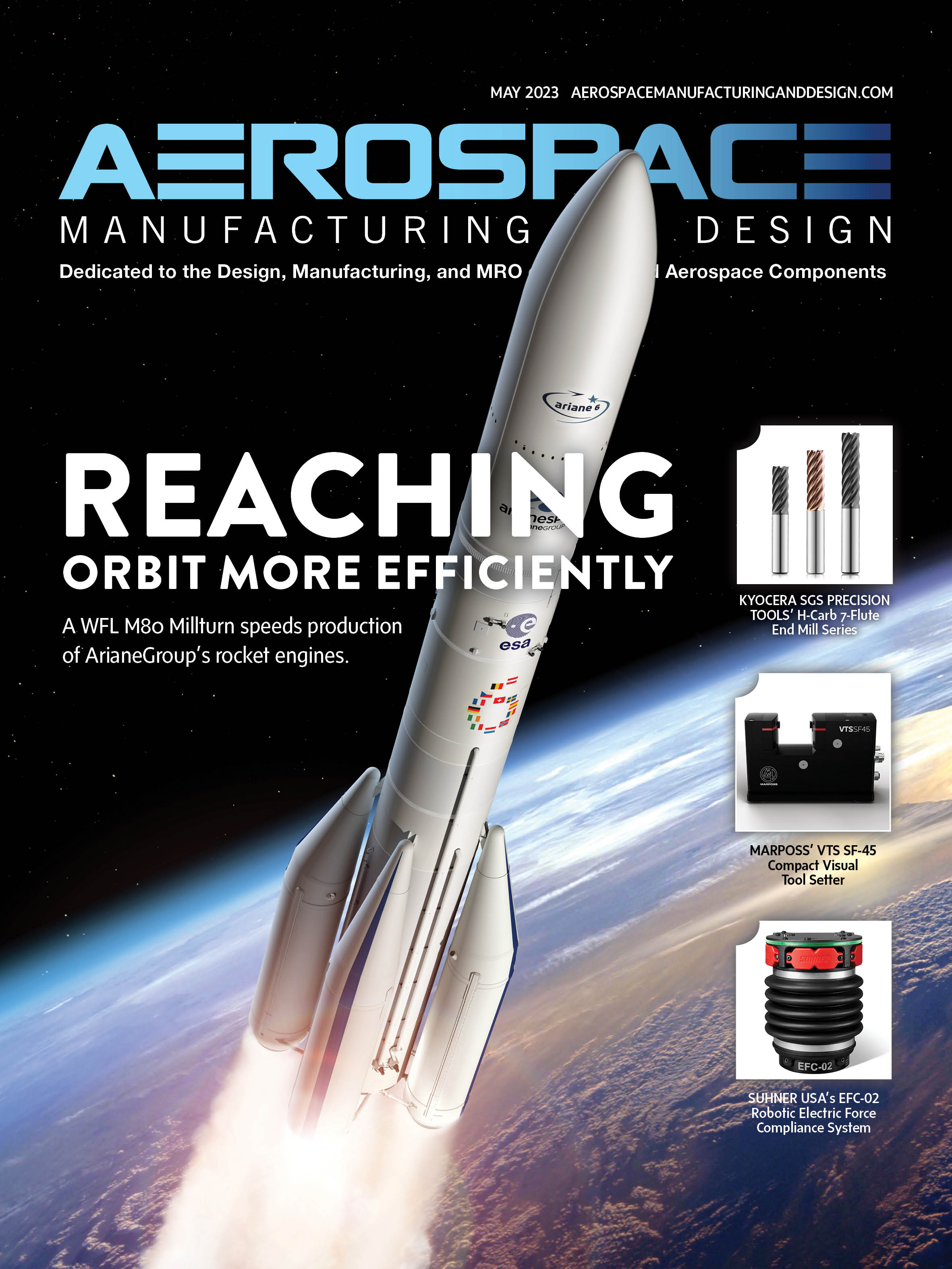
Explore the May 2023 Issue
Check out more from this issue and find you next story to read.
Latest from Aerospace Manufacturing and Design
- NIAR to add electric aircraft test capability
- Arnold Magnetic Technologies' custom electromagnetic capabilities
- Garmin earns best supplier recognition from Embraer for 9th consecutive year
- Dillon Manufacturing's Carbinite coating
- #43 Manufacturing Matters - 2024 Spring Aerospace Industry Outlook with Richard Aboulafia
- US operator UrbanLink orders 20 Lilium Jets
- TJ Davies’ retention knobs
- Mazak's VC-Ez 16X for aerospace machining