

As technology advances at a rapid pace, the aerospace industry is integrating digital technologies, automation, and data exchange in manufacturing processes. While Industry 4.0 brings numerous benefits and efficiencies, it also introduces new cybersecurity challenges, especially in the realm of operational technology (OT) cybersecurity.
OT encompasses the physical equipment and processes used to manage industrial operations, manufacturing, and critical infrastructure. In aerospace manufacturing, this includes control systems, sensors, and other devices responsible for managing and monitoring physical systems. OT cybersecurity focuses on protecting these assets from threats that can compromise safety, cause physical damage, or disrupt operations.
Unlike information technology (IT) cybersecurity, which primarily deals with protecting data and information systems, OT systems operate in real-time and directly control physical processes. OT systems are designed to operate for long periods with minimal maintenance, making them more susceptible to cyber threats. Attackers targeting OT systems aim to exploit vulnerabilities that can result in catastrophic consequences, including the compromise of aircraft systems or disruption of ground support systems.
Take stock of cybersecurity maturity
Gather your security team and ask a few questions to evaluate current readiness and maturity:
- Do your facilities teams understand what an attack could look like for your organization? Do you know the most common threat scenarios in your industry and how your defenses are aligned to protect your enterprise?
- Do you have a comprehensive incident response plan vetted by OT and IT teams; practiced and adjusted; and communicated between all the stakeholders?
Once you benchmark progress on these topics, consider leveraging the SANS Five Critical Controls for Effective OT Cybersecurity as a guide for prioritizing next steps. The five critical controls put a strong emphasis on practices that facilitate an active defense as opposed to a t raditional prevention-focused approach. The controls include:
Incident response plan: Create a dedicated plan that includes the right points of contact, such as which employees have which skills inside which plant, as well as thought-out next steps for specific scenarios at specific locations. Identify responsible parties, notifications, and escalation policies. Leverage tabletop simulation exercises to test and improve response plans.
Defensible architecture: OT security strategies often start with hardening the environment – removing extraneous OT network access points, maintaining strong policy control at IT/OT interface points, and mitigating high risk vulnerabilities. More important than a secure architecture are the people and processes to maintain it. The resources and technical skills required to adapt to new vulnerabilities and threats should not be underestimated.
ICS network visibility and monitoring: A successful OT security posture maintains an inventory of assets, maps vulnerabilities against those assets (and mitigation plans), and actively monitors traffic for potential threats. Visibility gained from monitoring your industrial assets validates the security controls implemented in a defensible architecture. Threat detection from monitoring allows for scaling and automation for large and complex networks. Additionally, monitoring can also identify vulnerabilities easily for action.
Secure remote access: A key method, multi-factor authentication (MFA), is a rare case of a classic IT control that can be appropriately applied to OT. Implement MFA across your systems of systems to add an extra layer of security for a relatively small investment. Where MFA isn’t possible, consider alternate controls such as jump hosts with focused monitoring. The focus should be placed on connections in and out of the OT network, not connections inside the network.

Risk-based vulnerability management: More than 1,200 OT-specific vulnerabilities were released in 2022, most of them with incomplete or erroneous information. While patching an IT system such as a worker’s laptop is relatively easy, shutting down a plant has huge costs. An effective OT vulnerability management program requires timely awareness of key vulnerabilities that apply to the environment, with correct information and risk ratings, as well as alternative mitigation strategies to minimize exposure while continuing to operate.
Importance of visibility
During 2022, Dragos uncovered 89% of manufacturers had limited visibility, making them easier targets for threat actors, and hampering their productivity and efficiency.
OT asset visibility enables manufacturers to monitor network traffic, detect unauthorized access attempts, and identify potential cyber threats or anomalies within the OT environment. It helps identify deviations from normal behavior, such as unusual network traffic patterns or unauthorized changes to device configurations, allowing for early detection and response to potential cyber incidents.
Limited visibility means a facility is only monitoring the IT to OT boundary, and not activity inside the OT network. Full visibility is achieved when network and device logs are centralized and can correlate various segments with network traffic analysis and asset inventories. Visibility comes in various forms from asset visibility to data flow inspection, but it can be summarized as anything increasing the defender’s knowledge of their environment. It often starts with asset inventory but must also include network monitoring and device logs.
In addition to the cybersecurity benefits, OT asset visibility can also help manufacturers achieve:
Enhanced operational efficiency: Aerospace manufacturing involves a complex ecosystem of interconnected OT assets, including control systems, sensors, machinery, and equipment. Having comprehensive visibility into these assets enables manufacturers to monitor performance, identify bottlenecks, optimize processes, and enhance overall operational efficiency (OEE). By tracking asset health and utilization, manufacturers can proactively address maintenance needs, schedule downtime efficiently, and minimize production disruptions.
Improved maintenance and reliability: Manufacturers rely on the continuous and reliable operation of critical assets to ensure smooth production processes and high-quality standards. OT asset visibility allows manufacturers to monitor asset health in real-time, detect anomalies or potential failures, and proactively schedule preventive maintenance. Identifying issues early can avoid unexpected breakdowns, reduce downtime, and optimize maintenance efforts.
Enhanced safety and compliance: OT asset visibility plays a vital role in ensuring the safety of personnel and operations. By monitoring asset performance, you can detect safety-critical deviations or abnormalities that could lead to accidents or hazardous situations. Visibility also helps teams track compliance with regulatory standards and industry best practices, ensuring assets and processes adhere to necessary safety guidelines.
Efficient resource allocation: OT asset visibility provides valuable insights into asset utilization, performance, and energy consumption. By understanding how assets are utilized and identifying potential inefficiencies, manufacturers can optimize resource allocation, reduce energy consumption, and minimize operational costs through energy-efficient scheduling, equipment consolidation, or identifying underutilized assets.
Better decision-making: Equipping aerospace manufacturers with accurate, real-time data about their production processes enables informed decision-making, such as identifying opportunities for process improvement, optimizing workflow, allocating resources effectively, and ensuring timely delivery. It empowers manufacturers with the necessary insights to make strategic decisions that drive productivity, quality, and profitability.
Effective OT cybersecurity is a journey, and it can take a long time for companies to build and implement a holistic, comprehensive cybersecurity program. There are deeply rooted challenges in protecting OT environments, and the complexity of the ever-changing threat landscape makes it even more difficult. By prioritizing OT asset visibility and implementing robust cybersecurity measures, aerospace manufacturers can protect physical assets, ensure the safety and reliability of systems, and maintain efficient operations.
Dragos
International Society of Automation (ISA)
About the author: Jennifer Halsey is senior industry marketing manager at cybersecurity company Dragos and a member of ISA, a non-profit professional association of engineers, technicians, and management engaged in industrial automation. She can be reached at jhalsey@dragos.com.
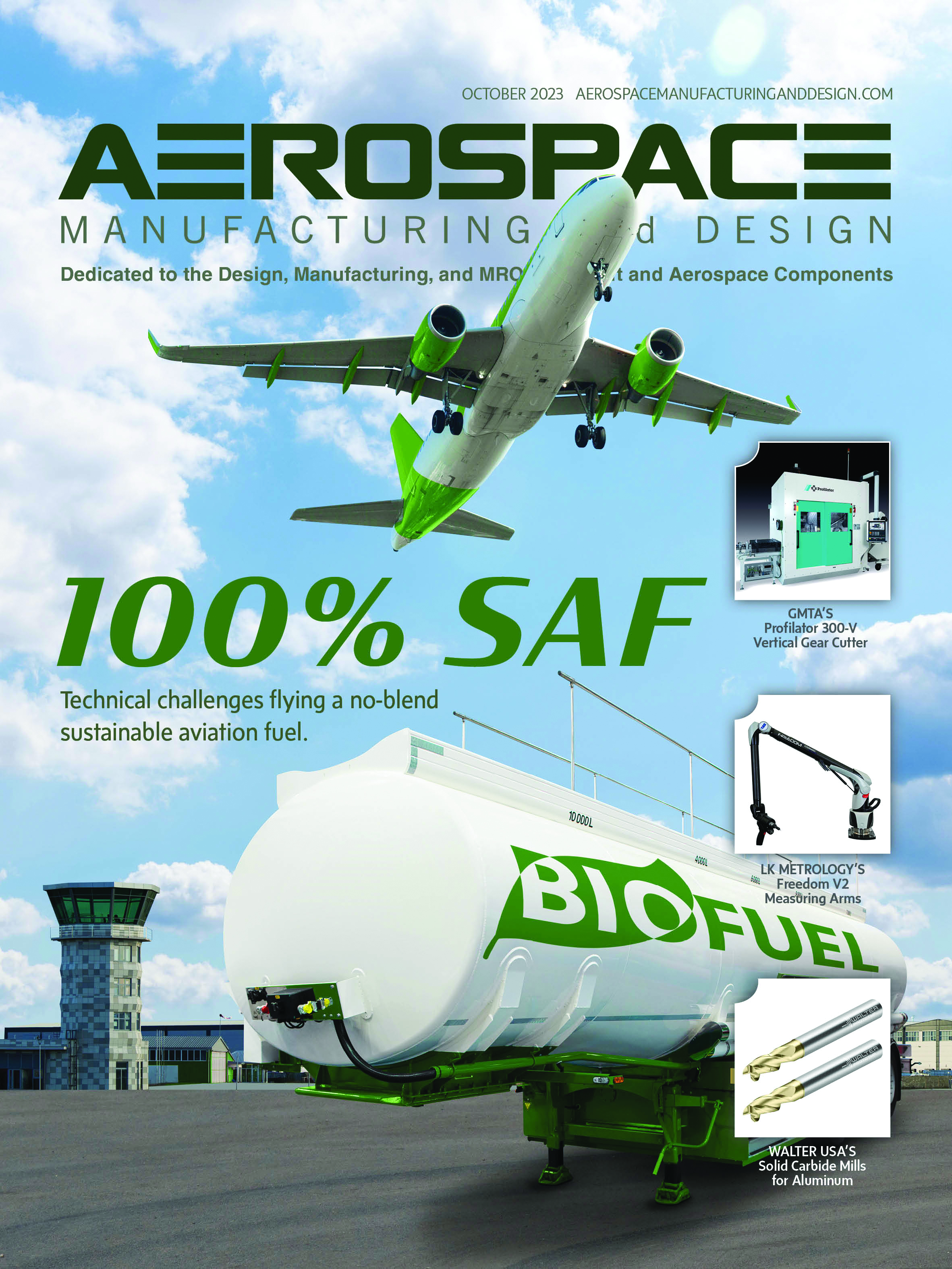
Explore the October 2023 Issue
Check out more from this issue and find your next story to read.
Latest from Aerospace Manufacturing and Design
- Upcoming webinar to highlight the rise of electric vehicles
- JEKTA, ZeroAvia partner on hydrogen-electric amphibious aircraft
- Mastercam 2025 software
- IMTS 2024 Conference: Cutting Edge Innovations: Maximizing Productivity and Best Practices with Superabrasives
- Eve Air Mobility unveils first full-scale eVTOL prototype
- Dillon Manufacturing's Fast-Trac Jaw Nuts
- IMTS 2024 Conference: Breaking the Tradeoff: Utilizing Deep Learning AI with X-ray Computed Tomography for Unparalleled Clarity and Speed
- #47 - Manufacturing Matters - The Ins and Outs of CMMC 2.0 with Smithers Information Security Services