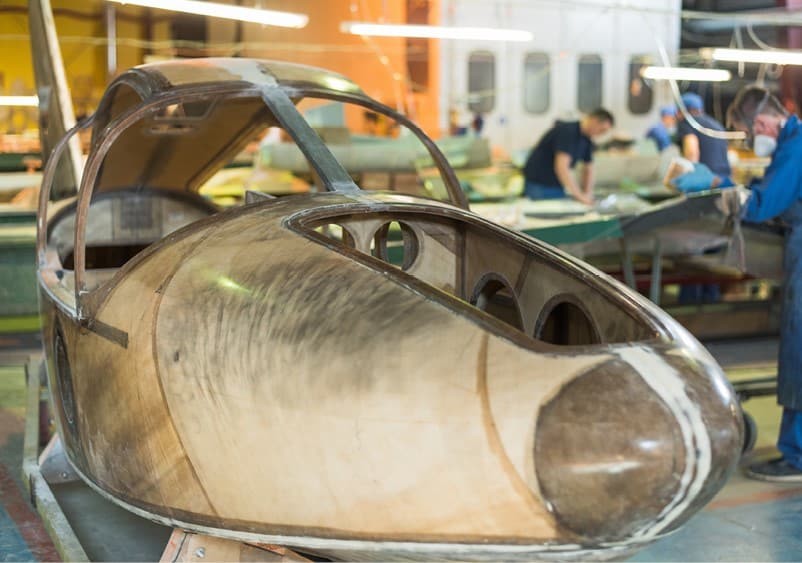
There are two principal ways to improve factory operations: automate or optimize the performance of people. Manufacturers have automated much during the past several decades, but many tasks aren’t yet fit for automation as machines don’t exist to do the precise or complex tasks humans perform.
Our recent survey shows manufacturers are investing in technology, including factory infrastructure such as cloud, edge, 5G (58%); automation (cobots, robots, etc.) (41%); and Internet of Things (IoT)/connected factory technology such as digital twins (38%). But only 33% of respondents were investing in human- centric technology such as virtual or augmented reality (VR/AR) and sensors.
The technology
Drishti has developed artificial intelligence (AI)-powered video analytics technology for manual assembly lines that’s purpose-built to identify areas where individuals are already performing above expectations and translate that to standardized work. It can review processes at a systems level and determine where people need more help, whether in the form of a process change, materials feed, spot training, or another effort. We’ve seen an efficiency increase of 11% and a 30% reduction in defects on lines where Drishti is deployed.
The name Drishti comes from the Sanskrit word meaning vision. It’s also a play on words for computer vision, which is a key technology in our platform. We chose the word because we provide manufacturers with the ability to see new perspectives of their operations, allowing them to make improvements in productivity, quality, and training at a granular level and at a broad scale. Drishti installs a camera above each assembly line station that live streams video to the cloud, where our action recognition technology tracks what occurred with the sequence and timing of each step. The AI acts as the brain, the computer vision acts as the eyes, and both work together to pull information from the live video streams. The data and insights populate dashboards, highlighting bottleneck locations and why they exist. Engineers, supervisors, trainers, and line associates use this systems-level data to make better decisions, at the right time, faster – with each data point backed by video.
Line optimization
Elite manufacturers marry technology such as AI, which sheds light on the problems that exist, and humans, who use their massive capacity to think and solve problems, to get the best of both worlds.
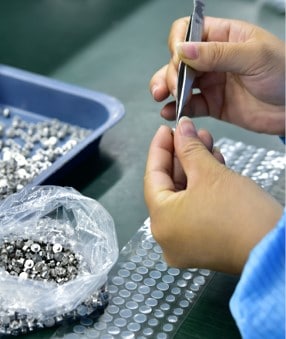
When a Tier 1 supplier decided to work with us, they selected an already highly optimized line for the pilot to validate whether Drishti could help reach the next level of performance.
They figured the only thing left to optimize on the pilot line was adherence to standardized work. Drishti empowered them to see there was far greater potential in optimizing the manufacturing system.
For example, there was significant value in eliminating micro stops, which were predominantly caused by the inbound material flow. When Drishti provided this data and video evidence, the engineering teams could introduce simple countermeasures, such as a revolving rack or someone feeding the worker material, and they gained a minute each hour. By compounding cases such as these, the supplier increased productivity 7% – on a line thought to be at its potential.
Not just for assembly lines
We are working mainly with manufacturers with manual assembly operations. However, all our technology needs to work is an unobstructed view of the activities being performed, repetitive movements that we can capture and measure, a stationary position to mount the cameras, and an Internet connection to transfer data.
Training and retention
Drishti can provide video-based training, so line associates perform at their most efficient with the fewest number of defects. This on-the-job, in-context training is more effective than written manuals and photos with captions. With video-based standardized work instructions, best practices are captured and disseminated anywhere.
People certainly haven’t reached their peak performance; they simply need manufacturers to invest in new technology that augments their efforts and helps them truly shine.
Drishti Technologies Inc.
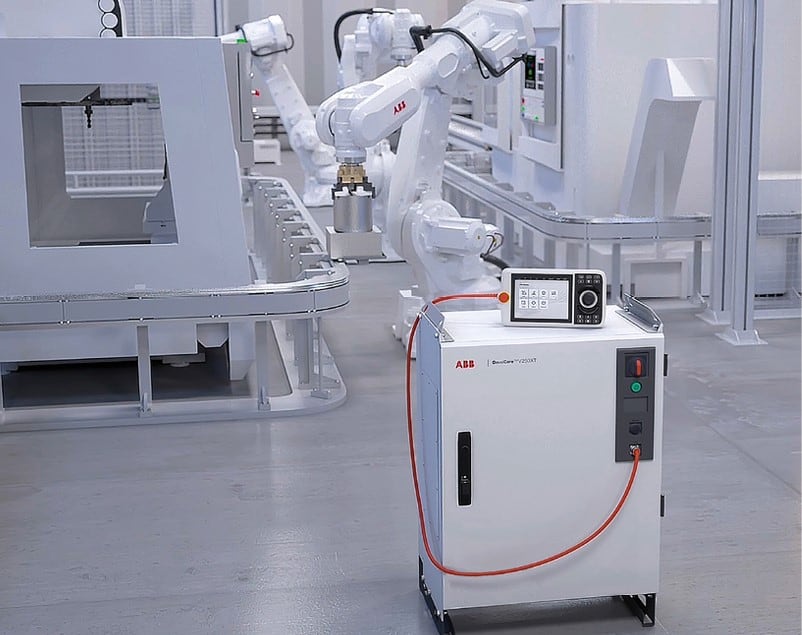
Robot controllers enable faster, scalable, more energy efficient manufacturing
OmniCore E10 and V250XT controllers offer motion control, 20% energy savings, future-proofing through built-in digital connectivity, and more than 1,000 additional functions for enhanced robot control for electronics assembly, logistics, and general manufacturing.
The controllers offer increased scalability through more than 1,000 hardware and software functions for programming, offline commissioning, simulation, maintenance, vision, and safety. They also feature built-in connectivity to ABB Ability Connected Services cloud-based service suite for robots, improving performance through enhanced predictive maintenance and lifecycle management. Both controllers are used with ABB’s FlexPendant hand-held controller.
The IoT Gateway open automation software for OmniCore makes joined-up production with seamless transmission of data from the factory floor, machine to machine (M2M), robots to other machines, and robots to sensors, to the MES/ERP system, or to the cloud.
ABB’s TrueMove and QuickMove motion control technology offer lower cycle times, high speed, position repeatability, and path accuracy, enabling robots to operate up to 25% faster than their predecessors.
The E10 is for confined space and high-density production lines with a 19" rack-mount design for small parts assembly and material handling. The controller powers SCARA robots and articulated robots with payloads up to 11kg, such as the IRB 920T and IRB 1300.
Designed to power articulated robots with a payload up to 300kg, such as IRB 6700, the OmniCore V250XT controller offers a versatile and powerful solution for logistics and general industrial applications. https://global.abb/group
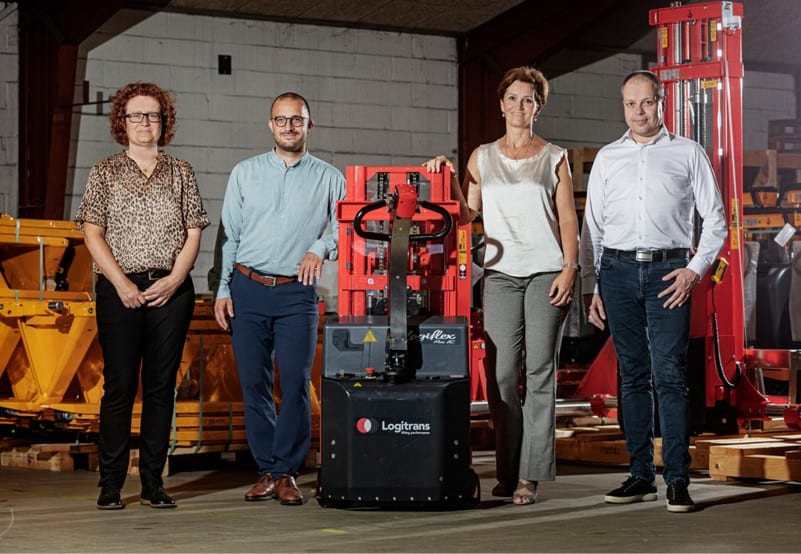
Mobile Industrial Robots (MiR) and Logitrans collaborate to build autonomous pallet jacks
Autonomous mobile robot (AMR) provider Mobile Industrial Robots A/S (MiR) and material handling equipment manufacturer, Logitrans A/S entered a strategic collaboration to build autonomous pallet jacks. Designed to fill a gap in the market for safely, efficiently, and autonomously lifting pallets directly from the ground, the autonomous pallet jack will combine MiR’s autonomous navigation and software capabilities with the functionality of electric pallet jacks developed by Logitrans.
The companies will develop a new range of autonomous pallet jacks that will supplement MiR’s current heavy-payload mobile robots, transporting pallets and goods smoothly and safely among people and other transport equipment in dynamic surroundings. MiR’s existing robots can pick up pallets from specially designed pallet racks, and customers are requesting AMRs that can pick up and deliver pallets from the ground.
MiR and Logitrans also plan to make a fully automated and a semi-automated autonomous pallet jack to fulfill different needs in the logistics processes. The long-term and strategic initiative of establishing new business areas and products for both MiR and Logitrans leverage the high-quality hardware equipment of Logitrans and the same advanced navigation technology and sophisticated fleet software as MiR’s traditional AMRs. https://www.mobile-industrial-robots.com; http://www.logitrans.com
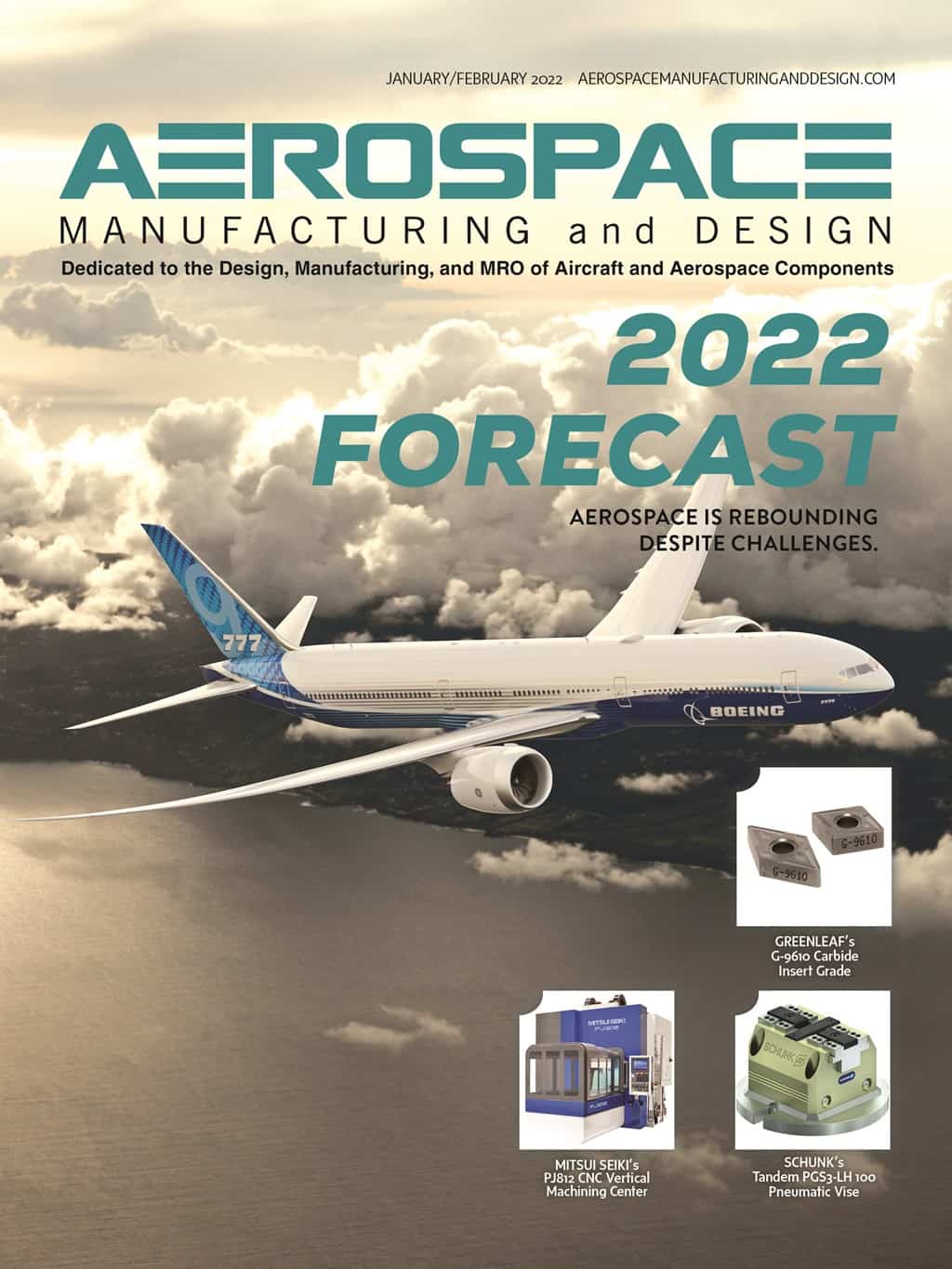
Explore the January February 2022 Issue
Check out more from this issue and find your next story to read.
Latest from Aerospace Manufacturing and Design
- Aura Aero selects Florida manufacturing, assembly site
- EMUGE-FRANKEN's high performance end mills
- IMTS 2024 Booth Tour: Engis Corporation
- How can we make electric vehicles more user-friendly?
- Leaders in Manufacturing webinar will ease your fears about changes in the industry
- October Lunch + Learn with EMUGE-FRANKEN USA and Okuma America
- October Lunch + Learn with SMW Autoblok
- marcus evans announces the Aerospace & Defense Manufacturing and R&D Summit 2024