The news released early last December that scientists and engineers at the Lockheed Martin Advanced Technology Center (ATC) in Palo Alto, Calif., had developed the lightest satellite cooling system (cryocooler) ever built was a revelation. Here was a heat-rejecting device weighing a mere 11oz, one-third the size of its predecessors, with an operating life of at least 10 years. Such a device would be highly desirable for anyone requiring a small cooler for IR sensors on platforms such as CubeSats or small UAVs. The press release contained few details, and begged more questions, which the developers of this technology consented to answer for AMD.
Ted Nast, Lockheed Martin fellow at the ATC in Palo Alto, and Dr. Jeff Olson, the principal investigator, offered these details of the microcryocooler:
“The microcryocooler was developed in response to recognized needs for a cryocooler with very low mass, high efficiency, and very long lifetime. Tactical applications include portable infrared cameras, and sensors in aircraft and UAVs. Space applications include Smallsat and CubeSat science and remote sensing missions, sensors for planetary missions (such as IR spectrometers for Mars landers), and in-situ resource utilization (such as atmospheric CO2 freezing for oxygen generation on Mars).”
The developers report that the microcryocooler provides up to 2W of cooling power to a payload, e.g. focal plane, through its cold tip operating in a temperature range of 100K to 200K. The dual-piston compressor drives gas oscillations to the cold finger through a transfer line. Gas dynamics within the cold finger and gas reservoir cause the cold tip to cool to cryogenic temperatures. The compressor is electrically powered through a standard electrical interface. The cryocooler weighs 310g (11oz), and is 115mm long from cold tip to gas reservoir.
“Unique in its combination of size and reliability, the microcryocooler follows a scalable and proven design for flight hardware systems,” the scientists say.
The tiny cooler’s small size does come with a small cost in thermodynamic efficiency. “The microcooler is somewhat less efficient than larger cryocoolers, requiring about 30% more input power for the same cooling power,” the scientists note. “The components were simplified and scaled down in size in order to preserve the same functionality while still being manufacturable.”
While the smaller cooler is capable of smaller input power and smaller cooling loads than larger coolers, the developers also note that the cooling required for IR cameras has also been reduced in recent years, enabling the use of the microcryocooler in a broad application set.
Such potentially game-changing devices do not come without precedent, and the scientists relate that the microcryocooler has been in development for the past 5 years by a core team of 10, comprised of cryogenics experts plus engineering and production support. They add that it leverages significant prior work from the team’s scalable design cryocooler development.
Good news for the aerospace community is that Lockheed Martin is making this cooler commercially available. “We are currently executing on contracts for microcryocooler deliveries in support of the Army for tactical applications and JPL for space applications,” the developers note. As for cost, “Prices are provided upon request by contacting Lou Borrego at Louis.j.borrego@lmco.com.”
Both of the principal investigators are able to comment on the development and applications. Ted Nast can be contacted at ted.nast@lmco.com, and Jeff Olson can be contacted at Jeffrey.r.olson@lmco.com.
About the author: Eric Brothers is senior editor of AMD and can be reached at 330.523.5341 or ebrothers@gie.net.
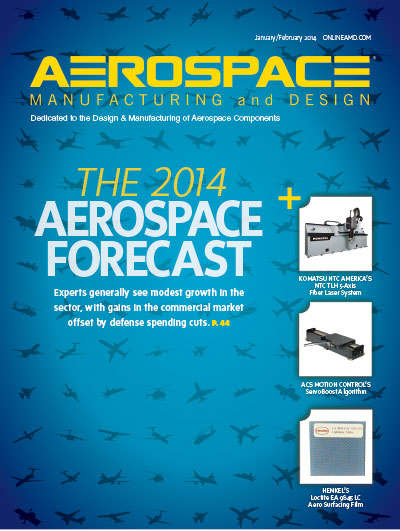
Explore the January February 2014 Issue
Check out more from this issue and find you next story to read.
Latest from Aerospace Manufacturing and Design
- UPCOMING WEBINAR: Additive Manufacturing for Aircraft Cockpit Interior Components
- Still time to register for the May 16 Manufacturing Lunch + Learn
- NIAR to add electric aircraft test capability
- Arnold Magnetic Technologies' custom electromagnetic capabilities
- Garmin earns best supplier recognition from Embraer for 9th consecutive year
- Dillon Manufacturing's Carbinite coating
- #43 Manufacturing Matters - 2024 Spring Aerospace Industry Outlook with Richard Aboulafia
- US operator UrbanLink orders 20 Lilium Jets