

With jet engine temperatures reaching more than 1,000°F, shaft speeds climbing well above 30,000rpm, and the extremely dry atmosphere at high altitudes, engineers face several design challenges.
When designing rubbing mechanical components such as bearings, seals, rotors, or valves for severe conditions, typical oil or grease lubrication often won’t suffice. Constant lubrication application is not always practical, and most lubrication would likely burn up shortly after being applied. So, the materials in these applications need to be self-lubricating, and aerospace engineers often turn to arguably the most versatile self-lubricating material available – high-temperature graphite.
Carbon graphite manufacturers have developed new carbon grades that withstand higher temperatures, drier atmospheres, and higher speeds and loads with better lubricating properties, benefitting jet engine manufacturers tasked with finding materials to optimize three variables:
Often, improving one of these variables will negatively impact another. For instance, increasing the size of the engine’s nacelle will typically increase air flow through the turbine and ultimately thrust. However, the cost of use and ease of maintenance will usually be negatively affected since a larger nacelle is heavier and has more areas that are not easily accessible. It is rare to find design opportunities that will positively affect all three of these factors simultaneously, such as self-lubricating, high-temperature graphite.
Engine thrust, efficiency
Optimizing wear resistance – In dry running applications, graphite’s coefficient of dynamic friction (COF) is about 0.10 to 0.25, attributed to the layered structure of the graphite grains within this material.Graphene layers improve dry running – On a microscopic level, graphene layers slide over each other and deposit a burnished film between the graphite and its counter face. This film protects the graphite from roughness on the counter face and is critical in optimizing dry wear resistance. Carbon graphite manufacturers can enhance this film with a film-former impregnation, resulting in a more robust film with excellent dry running capabilities.
High thermal conductivity reduces hot spots – While reducing shaft friction, graphite can dissipate heat from locations such as the interface between a bearing and a shaft due to high thermal conductivity – as high as 45BTU/hr·ft·°F. This helps prevent bearing friction from creating localized hot spots in an already hot environment that ultimately degrades bearing performance. Minimizing hot spots by using graphite bearings allows for improved performance in temperatures that would severely compromise the integrity of most other bearing materials.
Dimensionally stable, non-galling prevents shaft seizure – With no atomic attraction to a metallic shaft, graphite is non-galling and will not cause shaft seizure. Unlike many engineered plastics or metals, graphite does not soften nor deform, so the only major concern at extreme temperatures is oxidation. Graphite is also dimensionally stable and will not extrude outward when under pressure.

Weight reduction
Optimizing thrust efficiency of jet engines has a direct impact on cost of use, making graphite’s properties desirable.
Unnecessary weight added to a plane’s turbines will increase the amount of fuel needed. Graphite is lightweight, so replacing non-graphite mechanical components with graphite lowers costs.
Graphite bearings can be more than 4x lighter than bronze bearings of the same dimensions. Although a small constituent of a jet engine, weight reductions add up throughout time.
Ease of maintenance
Proper jet engine maintenance is critical for safety, so it is important to design for maintenance ease without sacrificing safety.
Graphite’s wear resistance allows it to endure substantial speeds and loads for extended periods of time. In dry running applications, it can withstand PV values – the product of the speed in ft/min and the load in pounds-per-square-inch (psi) commonly used to predict wear rates of mechanical components – higher than 30,000psi·ft/min with maintenance intervals of more than 20,000 hours.
High-temperature oxidation resistance – Modern jet engines are being built to run at higher temperatures to increase efficiency. As the temperature rating of all other turbine components increases, it is important that mechanical components keep up. A jet engine’s internal temperature is limited only by the lowest temperature-rated component.The future of high-temperature graphite
Graphite development is driven by the demand for materials that can withstand higher temperatures, more intense loads and speeds, and longer duty cycles. Carbon graphite manufacturers are working to develop modernized and advanced processes that push the limits of the material. These advances benefit the aerospace industry since aerospace engineers deal with arguably the most extreme application conditions of any industry.
Metcar (Metallized Carbon Corp.)
https://www.metcar.com

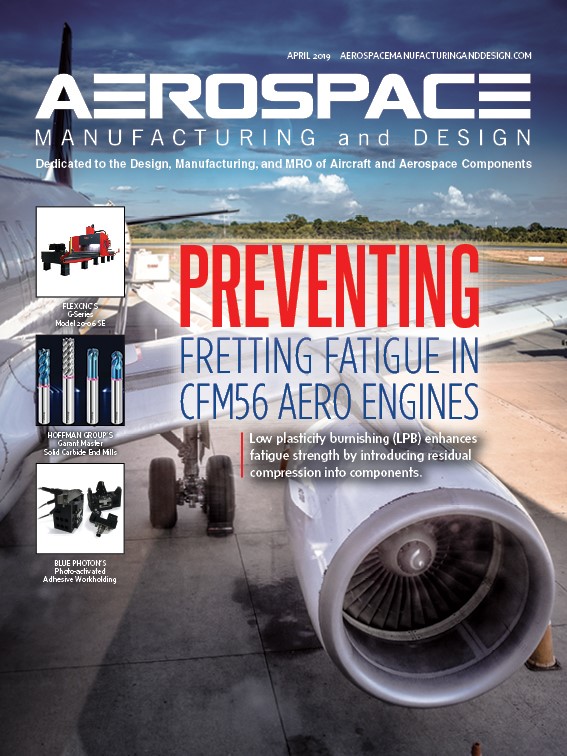
Explore the April 2019 Issue
Check out more from this issue and find your next story to read.
Latest from Aerospace Manufacturing and Design
- Upcoming webinar to highlight the rise of electric vehicles
- JEKTA, ZeroAvia partner on hydrogen-electric amphibious aircraft
- Mastercam 2025 software
- IMTS 2024 Conference: Cutting Edge Innovations: Maximizing Productivity and Best Practices with Superabrasives
- Eve Air Mobility unveils first full-scale eVTOL prototype
- Dillon Manufacturing's Fast-Trac Jaw Nuts
- IMTS 2024 Conference: Breaking the Tradeoff: Utilizing Deep Learning AI with X-ray Computed Tomography for Unparalleled Clarity and Speed
- #47 - Manufacturing Matters - The Ins and Outs of CMMC 2.0 with Smithers Information Security Services