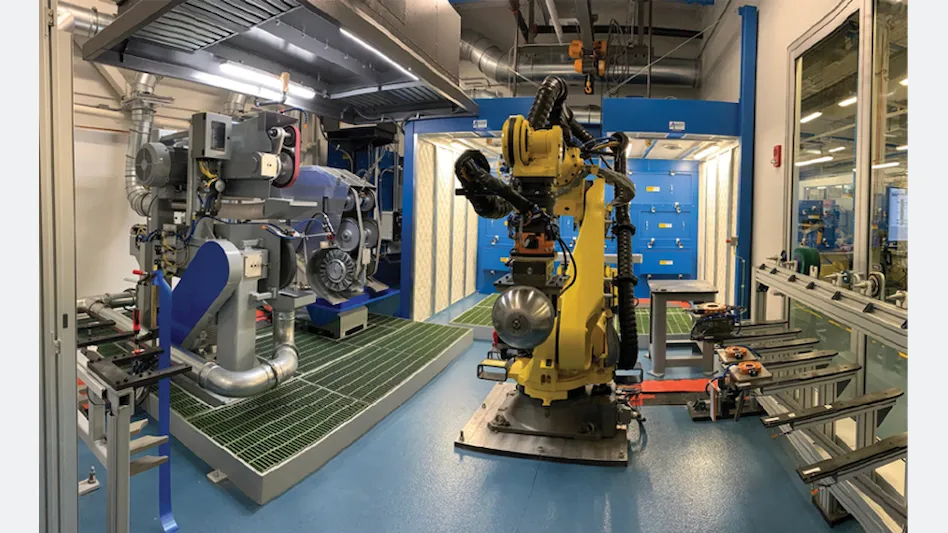
Norton | Saint-Gobain
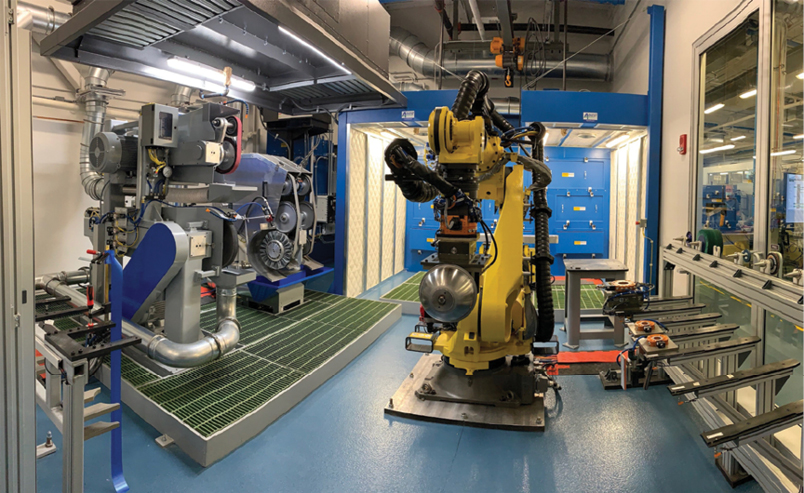
Challenging grinding and machining operations increasingly require custom solutions. It could be research and testing of new abrasives to improve quality or throughput, or trying an entirely new process, potentially disrupting current manufacturing. As manufacturers turn toward automation and Industry 4.0, the automation variable can present a lot of challenges, as well as opportunities.
To help customers develop innovative materials, processes, and automation, Norton | Saint-Gobain Abrasives has established its Abrasive Process Solutions (APS) program. The APS team has access to many assets to solve practically any material removal or surface generation problem. Abrasive process expertise along with access to the best equipment allows the APS team to offer useful grinding process development solutions to customers in aerospace, automotive, metal fabrication, medical, molding, and more.
The APS robotic automation cell at the heart of the APS program is one of the most comprehensive abrasive automation cells in the world, equipped for nearly any material removal or surface generation process. The capabilities of the automation cell include media-to-part and part-to-media applications; wet and dry processing; and use of coated, non-woven, bonded, and superabrasive products. The comprehensive array of services is combined with quick responses and short turnarounds on projects.
The team’s focus
This APS team is focused on solving customer problems, aiming to be an extension of the customer to provide essential services complementing their existing business.
For instance, if the customer has neither time nor ability to test a new part or process, the automation cell can be set up to do the testing for them. Testing at the APS lab will be conducted concurrent with the customer’s normal day-to-day tasks, not disrupting company output. The combination of access to the best equipment and expertise in many processes also ensures customers’ needs are met.
Similarly, if a customer has a part and is unable to process it themselves, the APS team can offer these services. A part may require a specific machine or process, and the significant investment in a machine for this may not be economically viable for some companies.
Outsourcing work has increased significantly, especially post-COVID-19, as companies may not have staff to develop processes for new parts or upgrade processes for existing parts. In these instances, experienced APS application engineers using the automation cell can assist.
Customer benefits
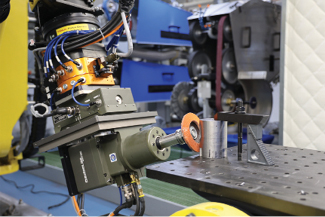
The APS robotic automation cell was built to handle just about any challenge a customer could face. The cell features a Fanuc R2000iC robot with a force sensor capable of being programmed to perform multiple tasks, including media-to-part and part-to-media solutions, plus wet/dry processing, and using various products already mentioned.
The APS cell also features a programmable pivot table, 6" deep coolant pans, abrasive tools, toolholders and radial compliant devices, spindle motors and compliance slides, and two heavy-duty grinding heads with 15hp to 40hp motors, respectively, with a programmable pivot head with dual belt and wheel setup capability.
This equipment facilitates processing large parts, with the pivot table and robot arm combining to ensure critical areas are reached for media-to-part applications. Belts, cut-off wheels, diamond wheels, and grinding wheels (among others) can be accommodated on the stacked head for part-to-media applications requiring heavy pressure, such as casting cut-off and gate grinding. A side-by-side spindle head can use two belts and up to four radial wheels, which allow precise finishing with buffing and filament brushes.
Working with the team
The APS team is an extension of the Norton application engineering group that’s been providing on-site customer support since 2004. Application engineers assist customers in applying and optimizing Norton abrasive products in the customer’s application. By showing added value through increased abrasive performance, lowering reject and scrap rates, and improving machine efficiency, application engineers help customers drive down the overall cost per part.
Armed with a verified abrasive process solution, customers can confidently approach one or more of the qualified original equipment manufacturer (OEM) integrators to implement the solution. This reduces customers’ risk and lets them further reduce expenses by shopping among various vendors, something not possible without the information the APS team provides.
Solutions

features two unique finishing heads.
If a company is experiencing a certain issue, Norton can take this issue, generate a custom solution, and show the client how to solve their problem. Customers receive a proven answer to their problem. Some examples of specific solutions that can be provided include:
Post-COVID-19 labor shortages – Companies simply don’t have the workforce to test new products and processes. The APS team gives these companies a solution that allows them to keep working efficiently without the commitment and expense of employing full-time specialized engineering staff.
Robotic arms – They can be used when it isn’t safe or feasible to have a human operator present. A robotic replacement may also be more cost-efficient in the long run as it takes human labor out of the equation. Reducing expenses is a key advantage the APS team can demonstrate.
Using an external lab can mitigate risk – If customers wish to test a new solution or process, they don’t have to stop existing production or overexert themselves. Costly in-house testing is avoided and customers receive a proven solution.
Data driven solutions – Using information provided from the APS team and automation cell testing, companies can shop for new equipment with the peace of mind they’re buying the correct equipment, while also not tied to one vendor.
Tackling abrasive challenges
The APS program brings a new abrasive process development and automation solution to customers. They have all the tools necessary to tackle any abrasive challenges customers may bring.
With the APS program, Norton | Saint-Gobain customers can receive customized solutions to problems they may not be equipped to handle.
About the authors: Tony Landes is abrasive process innovation manager, and Mike Shappell is application engineer IV, for Norton | Saint-Gobain Abrasives. To learn more about the APS program, contact the APS team at https://www.nortonabrasives.com/en-us/aps-information-request.
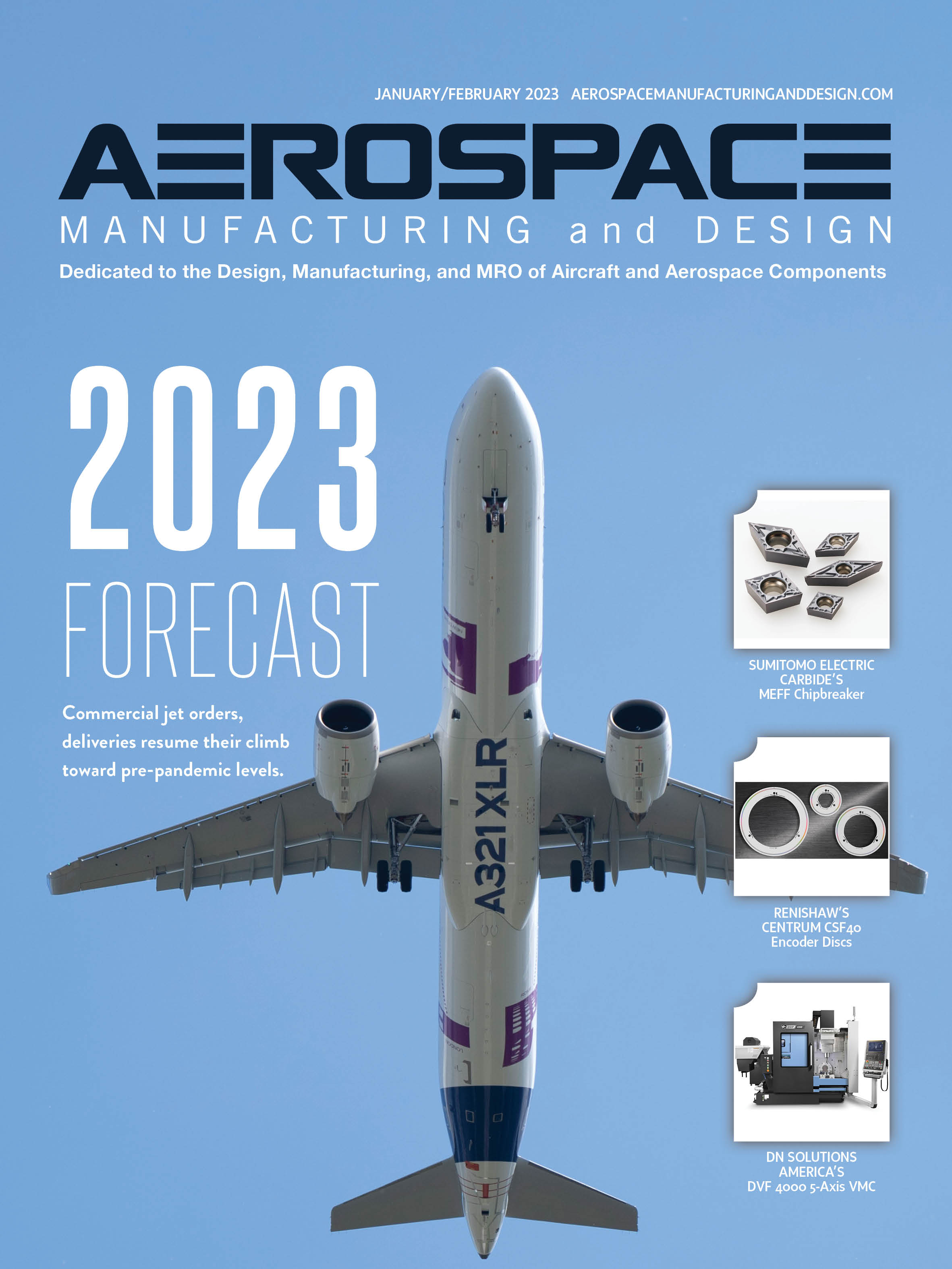
Explore the January February 2023 Issue
Check out more from this issue and find your next story to read.
Latest from Aerospace Manufacturing and Design
- JEKTA, ZeroAvia partner on hydrogen-electric amphibious aircraft
- Mastercam 2025 software
- IMTS 2024 Conference: Cutting Edge Innovations: Maximizing Productivity and Best Practices with Superabrasives
- Eve Air Mobility unveils first full-scale eVTOL prototype
- Dillon Manufacturing's Fast-Trac Jaw Nuts
- IMTS 2024 Conference: Breaking the Tradeoff: Utilizing Deep Learning AI with X-ray Computed Tomography for Unparalleled Clarity and Speed
- #47 - Manufacturing Matters - The Ins and Outs of CMMC 2.0 with Smithers Information Security Services
- Qatar Airways orders 20 more Boeing 777-9s