
O-rings are ubiquitous, uncomplicated sealing solutions for millions of products. They seal moisture and environmental contaminants out, separate surfaces to mitigate friction, and keep in essential fluids. However, despite their seeming simplicity, O-rings used in aerospace take on an unexpected level of material and performance complexity when engineering and design standards and industry regulations are factored into purchasing decisions.
The number of O-rings found on an average commercial jetliner reaches into the thousands, and each must compensate for different environmental conditions – high and low pressure, aggressive lubricants and fluids, extreme temperature changes, industrial performance requirements, and sometimes challenging installation procedures.
With no one-size-fits-all O-ring solution, manufacturers must rely on their suppliers’ material, testing, and industry expertise to identify the best seals for every use.
Dr. Robert W. Keller, with 38 years of experience in the specialty elastomer and sealing products industry, joined Freudenberg-NOK Sealing Technologies in 2005. Following, he answers five frequently heard customer questions.

1) Can a supplier quote a single part or package of parts?
In some cases, this is straightforward, such as with the AS3209-214, which is an industry-standard size O-ring with an industry-standard materials specification and Qualified Products list requirements. There’s also a large variety of customer-part number standards and drawings with customer-approved sources of supply. This requires researching customer drawings, dimensional tolerances, and materials specifications to assure that we have the correct dimensions and are authorized to supply the part or material. The vast number of industry standards and customer part series with hundreds of specific sizes in multiple materials makes this one of the most complex challenges with aerospace O-rings.
2) Can you help diagnose O-ring failure via a picture?
We also want details on the mating parts’ dimensions and tolerances. We also need as much application detail that can be provided – temperature extremes, pressure extremes, fluids and gases the ring is exposed to, and possibly assembly practices. We typically want to get the failed part(s) back for microscopic examination which usually provides a lot of information. Our 3D microscopes can measure dimensions and depth of any damage or unusual surface conditions of the O-ring. This is a typical question concerning O-rings installed in critical applications.
The most prevalent cause of leakage we see is installation damage. The O-ring is typically installed over metal splines, which can cut or gouge its surface. Likewise, misalignment of mating parts can cause localized pinching or cutting of the O-ring surface. Considering the millions of critical aerospace O-rings we ship per year, the actual incidence of failure is less than 0.04 parts per million O-rings produced and shipped.
3) Can you advise if an O-ring and gland design is appropriate?
Gland and O-ring designs that are very old and have been in place for many years should be reviewed. While there are many O-ring design software packages available, they don’t always take into account many of the variables and peculiarities of actual customer gland designs. Some software can also introduce numerical rounding and truncating, resulting in calculation errors. We can typically do a more thorough analysis with our in-house calculation routines and can factor in temperature extremes and coefficients of thermal expansion of the mating gland and O-ring material to get a more detailed look at the designs. Our in-house calculation routines can perform ‘what-if?’ calculations, and we can look at and recommend changes to gland design, O-ring dimensions, O-ring dimensional tolerance, or material recommendations.
Since O-rings are relatively inexpensive and physically compliant, we’ve seen them used as soft, conical seals or high-force shut-off seals in high-pressure hydraulic systems. This type of non-traditional application is considerably beyond what off-the-shelf software packages can calculate. Often, we need to perform finite element analysis (FEA) to fully understand how the O-ring will perform in these applications. So, we need as much detail about the application as possible – mating part dimensions and dimensional tolerances; materials the mating part is made from; fluid contact; pressure extremes for normal and proof testing; and temperature extremes. We have refined our techniques for elastomer property modeling and have found our FEA to be very accurate in predicting performance.
4) With typical fluids or gases that could interact with the O-ring, what would the best material be?
Parent industry standard materials specification or customer materials specifications will often define the material in sufficient detail. However, there are still questions that the industry standard or customer standard doesn’t address in detail. Our extensive library of the chemical compatibility of our materials with various fluids and gases is our first point of reference. If our library information doesn’t sufficiently answer the question, our laboratories can test to define the best elastomer material for the application.
It’s not uncommon for fluids, temperatures, and pressures to produce situations where no material exists in our current portfolio or our competitors’. We have extensive expertise and laboratories for developing newer, high performance materials. We typically pursue major aerospace materials development projects annually and we are currently finalizing development of an ethylene propylene diene monomer (EPDM) material with improved low-temperature performance for aircraft hydraulic systems and a fluoroelastomer (FKM) material with improved low-temperature flexibility for high-pressure aircraft fuel systems.
Enhanced low-temperature performance is currently a major technology driver in aerospace O-rings for higher altitude flight with prolonged low-temperature soak periods. Since the design is simple, most of the O-ring technology is in the material and material performance.

5) If an O-ring was designed to seal fluid X, but some customers use fluid Y in the field, what is the risk and should we replace the O-rings?
As much detail as possible about the different fluids, pressure extremes, and temperature extremes is typically needed. We may run cyclic accelerated aging studies to look at exposure to fluid X followed by exposure to fluid Y then back to fluid X or a mixture of both. We look at standard properties such as volume change, property degradation, or compression set resistance. Test results will determine if O-rings must be fully replaced or not.
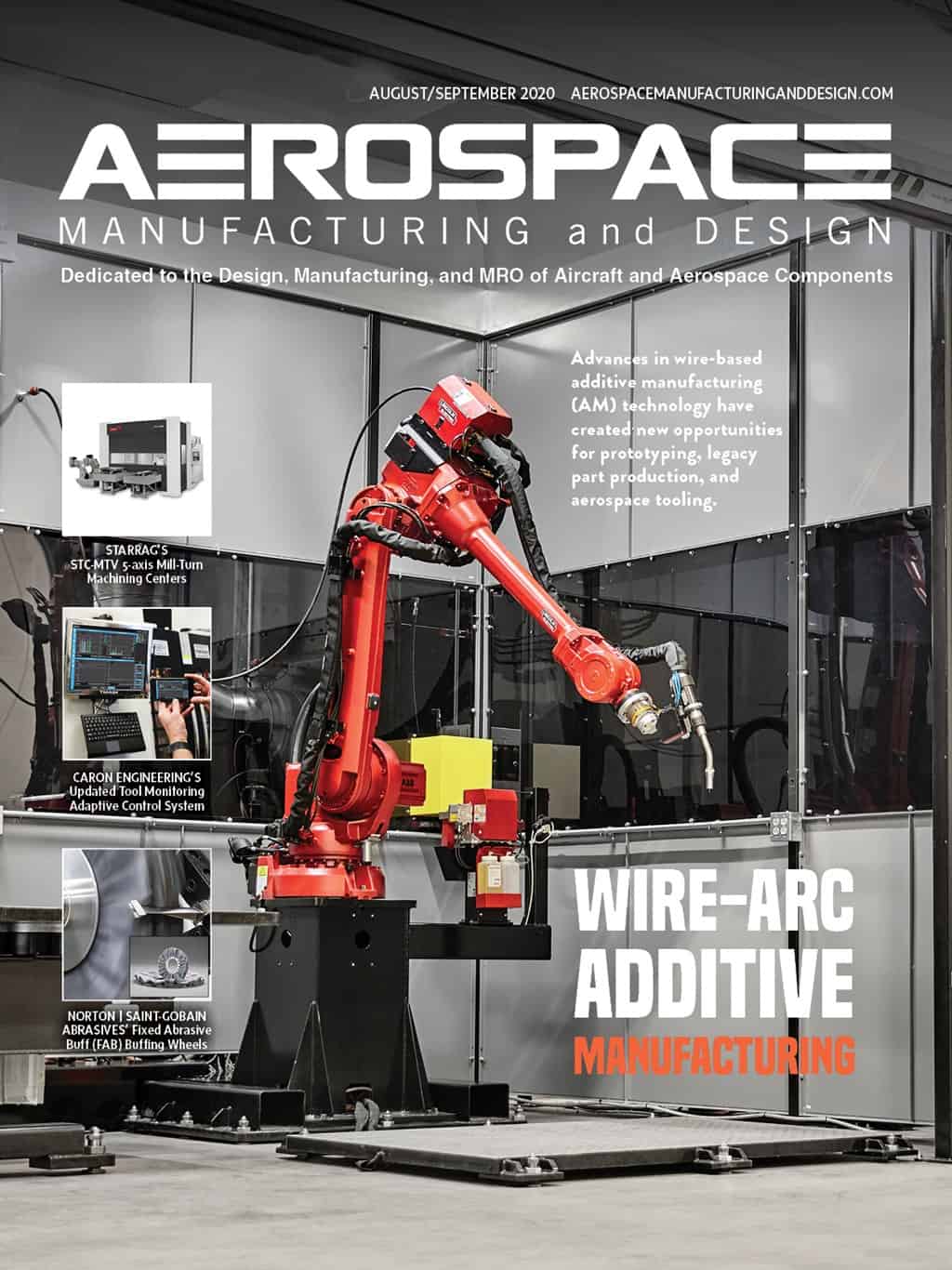
Explore the August September 2020 Issue
Check out more from this issue and find your next story to read.
Latest from Aerospace Manufacturing and Design
- Upcoming webinar to highlight the rise of electric vehicles
- JEKTA, ZeroAvia partner on hydrogen-electric amphibious aircraft
- Mastercam 2025 software
- IMTS 2024 Conference: Cutting Edge Innovations: Maximizing Productivity and Best Practices with Superabrasives
- Eve Air Mobility unveils first full-scale eVTOL prototype
- Dillon Manufacturing's Fast-Trac Jaw Nuts
- IMTS 2024 Conference: Breaking the Tradeoff: Utilizing Deep Learning AI with X-ray Computed Tomography for Unparalleled Clarity and Speed
- #47 - Manufacturing Matters - The Ins and Outs of CMMC 2.0 with Smithers Information Security Services