Grooving Tool Upgrades Added
Iscar has expanded several of their popular lines of grooving tools, which include the Helido Round H400, Helitang Upfeed tangential milling cutter, and the Cut-Grip grooving inserts for ID grooving.
The Helido Round H400 fine-pitch mills improve profile machining and ramping over a wider range of applications. Included are the 10mm and 16mm inserts, to complement the original 12mm insert. Matching cutters cover the 1.0" and 1.25" diameters for endmills, and 1.5" to 4" for facemills.
Unlike true rounds, Helido 400 Round inserts have a periphery that consists of bounding arcs with radii, normally found on pure rounds twice their size. Each insert has four 120o arcs. This enables the cutters to have more flutes compared to existing standards resulting in higher feed capability.
The new high-feed milling cutter extends the benefits of the Helitang Upfeed tangential milling cutters to ramping work as well. In tangential milling, the insert lies flat in the pitch circle, presenting its strongest cross section to the main cutting force vector. This permits much faster feeds and deeper cuts without risk of sudden insert failure. It also enables stronger cutters and finer pitch in a given-size cutter.
Key to the ramping capability is the Iscar FTP insert. The geometry, modified just enough to allow ramping, retains the proven high-feed capability of the Tangmill line. It features the familiar double sides with four peripheral ground cutting edges plus a shallow 12.5º entering angle. In the cutter, it fits rigidly into a standard tangential seat with dovetailed clamping. Inserts come with a choice of edge geometries for standard work or ETR geometry for heavier, higher feed applications.
The line of improved Cut-Grip grooving inserts for ID grooving feature the N-type chipformer. Internal groovers with the advanced chipformer are available for diameters down to 22mm (0.866").
Iscar Metals Inc.
Arlington, TX
iscar.com
Robust, Improved Control Software
Improvements to WinMax8 include advancements to existing features – making them more robust – and several new features resulting in four patent awards for Hurco.
UltiMotion’s 3D compensation of machine squareness, mechanical system dynamics, and advanced motion control improve the system accuracy. Hurco’s acceleration and vibration control system reduces vibration, resulting in a smoother motion without sacrificing speed, resulting in better surface quality and longer machine life.
UltiMotion’s rapid cornering capability allows the spindle to travel through corners at high speed with negligible deviation without overshooting or stopping. This is especially beneficial in reducing cycle time when machining parts. For rigid tapping, UltiMotion deploys a coordinated motion control mechanism that monitors the spindle angle at all times and controls the axes to follow the spindle position.
UltiMotion includes a proprietary dynamic variable look-ahead mechanism, which does not require a fixed number of blocks. Instead, the control evaluates the geometry and motion profile and makes sure there is enough lookahead information to make optimized maneuvers.
Other new features include UltiMonitor, Absolute Tool Length, and Tool Change Optimization. A free trial of WinMax8 is available at www.hurco.com/winmax.
Hurco Companies Inc.
Indianapolis, IN
hurco.com
Structural Void Filling Compounds
Scotch-Weld Structural Void Filling Compounds EC-3550 B/A FST and EC-3555 B/A FST changes the manufacturing of aircraft components. These low-density void fillers save time and money in aircraft production by eliminating process steps, reducing worker time, and increasing throughput. With a unique combination of easy dispensability and non-sag performance, Scotch-Weld low-density void filling compounds offer a number of productivity advantages.
These Scotch-Weld compounds are lightweight, extrudable, and pumpable, offering superior handling attributes and dispensability. The simplified preparation and cleanup for the compounds eliminates weighing, mixing, and potential re-packaging, saving significant production time. With fast, direct application, the products reduce – and in some instances, eliminate – hand troweling and trapped air, helping to avoid pinholes, voids, and porosity.
Scotch-Weld low-density filling compounds are fast-cure, non-brittle, non-sag materials that are easier to handle than traditional materials, resisting chip-outs and breakouts. The products’ non-sag properties allow application of the compound to multiple work pieces at one time. In addition, the products exhibit good paint retention and adhesive bond strength.
Along with cutting production costs and time, the compounds also help manufacturers comply with safety regulations for aircraft interiors. Stand-alone FR/FST compliance allows the products to pass inspection alone or in honeycomb panel construction. Formulation of the compounds is with non-halogenated and antimony-free flame-retardants. With less touch time and less cycle time, Scotch-Weld low-density void filling compounds help reduce part weight while cutting shop floor costs.
3M
St. Paul, MN
3M.com/LDVF
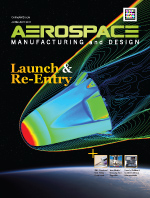
Explore the July 2011 Issue
Check out more from this issue and find you next story to read.
Latest from Aerospace Manufacturing and Design
- NIAR to add electric aircraft test capability
- Arnold Magnetic Technologies' custom electromagnetic capabilities
- Garmin earns best supplier recognition from Embraer for 9th consecutive year
- Dillon Manufacturing's Carbinite coating
- #43 Manufacturing Matters - 2024 Spring Aerospace Industry Outlook with Richard Aboulafia
- US operator UrbanLink orders 20 Lilium Jets
- TJ Davies’ retention knobs
- Mazak's VC-Ez 16X for aerospace machining